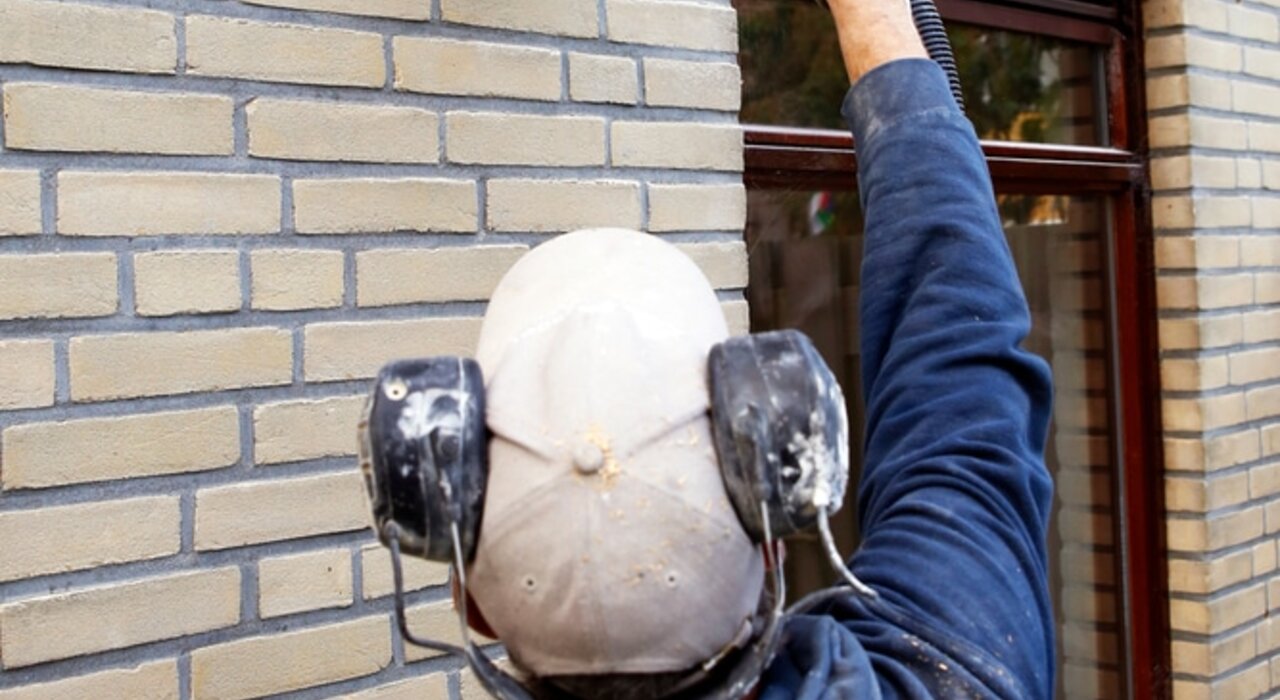
Cavity wall insulation is a common feature in many UK homes, designed to reduce heat loss and improve energy efficiency. While it offers significant benefits, there are notable problems associated with cavity wall insulation. Understanding these issues is crucial for homeowners and builders to ensure they maximise the benefits while minimising potential pitfalls.
Dampness and moisture problems in cavity wall insulation
Dampness and moisture issues within cavity wall insulation are prevalent and can lead to significant problems for both the structure of the property and the health of its occupants. These issues often stem from various factors, primarily poor installation and environmental conditions. When insulation is not correctly installed, it creates pathways for water to penetrate and become trapped within the wall cavity. Additionally, over time, external walls may develop cracks or sustain damage, allowing rainwater to seep into the cavity. Another common culprit is condensation, which occurs when the air inside the cavity condenses against the colder external walls, particularly in the absence of adequate ventilation. The type of insulation material used also plays a crucial role in how susceptible the cavity wall is to moisture. Materials like fibreglass and mineral wool can absorb moisture, which not only reduces their insulating effectiveness but also leads to internal wall dampness. Foam insulations, while generally more resistant to water absorption, can still pose moisture problems if not installed properly. The consequences of such dampness are far-reaching. Prolonged exposure to moisture can weaken the structural integrity of the walls, necessitating costly repairs. It also provides ideal conditions for mould growth, posing significant health risks, especially for individuals with respiratory problems. Moreover, wet insulation loses its thermal efficiency, leading to increased energy consumption and higher heating bills. Additionally, damp insulation can cause musty odours, diminishing the overall living environment within the property.
Mitigation
To prevent these issues, several measures need to be taken. Ensuring that insulation is installed correctly by a qualified professional is essential. This includes not only the proper fitting of the insulation but also a prior assessment of the property to determine the suitability of the insulation and the condition of the external walls. Maintaining adequate ventilation within the cavity can help mitigate condensation build-up. Regular inspections of the external walls and the insulation are also crucial in identifying potential issues early on, thereby preventing extensive damage. In regions prone to heavy rainfall or for properties particularly susceptible to moisture, opting for water-resistant insulation materials can be a wise decision.
[caption id="attachment_70163" align="aligncenter" width="640"] Problems with cavity wall insulation - damp[/caption]
Thermal bridging in cavity wall insulation
Thermal bridging is a significant concern in cavity wall insulation, often leading to reduced efficiency and various related problems. This phenomenon occurs when there are gaps or breaks in the insulation, creating pathways for heat to escape. These bridges typically form at junctions between walls, floors, and ceilings or around windows and doors. The issue can also arise from structural elements like steel or wooden beams that conduct heat more readily than the insulated areas. The impact of thermal bridging extends beyond just heat loss. These cold spots on the walls can become sites for condensation, as the warm, moist air inside the house comes into contact with the colder surface. This condensation can lead to mould growth, negatively impacting indoor air quality and potentially the health of the occupants. Furthermore, in extreme cases, continuous thermal bridging can lead to structural damage due to the prolonged exposure of certain building materials to moisture. The design and installation of insulation play a crucial role in mitigating thermal bridging. It’s essential that the insulation is continuous and covers all parts of the building envelope without gaps. Special attention should be given to the areas around windows, doors, and junctions, ensuring these are properly insulated. Using materials that have a lower thermal conductivity can also help in reducing the effects of thermal bridging. Moreover, modern construction techniques and materials are increasingly focusing on creating thermal breaks – sections of material with low thermal conductivity installed in the building envelope to prevent heat transfer. In retrofit situations, addressing thermal bridging can be more challenging. It often involves adding additional insulation or employing specific strategies to create thermal breaks. This might include installing insulated dry lining on the internal walls or using specially insulated plasterboard. For new constructions, the focus should be on design strategies that minimise thermal bridging right from the planning stage.
Degradation over time
The degradation of cavity wall insulation over time is a critical issue that affects not only the insulation's efficiency but also the overall structural integrity and energy efficiency of a building. This degradation can be attributed to a variety of factors. Moisture and water damage are among the primary culprits in insulation degradation. When insulation materials absorb moisture, they often lose their thermal properties. Continuous exposure to such conditions can lead to permanent damage, rendering the insulation ineffective. Additionally, environmental factors like air pollutants and UV radiation can cause chemical breakdown in some insulation materials, altering their structural integrity and insulating capabilities. Physical disturbances, such as building settling or renovations, can also compress or displace the insulation, reducing its effectiveness. Another significant factor contributing to insulation degradation is pest infestation. Rodents and insects can nest in insulation materials, causing physical damage through their activities. This not only leads to a reduction in the insulation's efficiency but can also create health hazards. The consequences of insulation degradation extend beyond reduced energy efficiency. It can lead to increased heating costs due to the loss of heat retention capabilities. Occupants may experience discomfort due to uneven heating or cooling within the home. Moreover, long-term degradation can contribute to issues like dampness and mould growth, potentially damaging the building's structure and interior finishes. To manage and mitigate the effects of insulation degradation, several measures are necessary. Regular inspections of the insulation are essential to identify early signs of degradation. Choosing high-quality, durable materials can significantly reduce the rate of degradation. Materials should be selected based on their resistance to the specific environmental factors of the building's location. The role of professional installation cannot be overstated; ensuring that the insulation is correctly placed and secured is crucial for its long-term effectiveness. Additionally, maintaining the building envelope, including the roof and external walls, can prevent issues like moisture ingress that accelerate insulation degradation.
Pest infestation problems with cavity wall insulation
Pest infestation within cavity wall insulation is a problem that can lead to significant issues, not only for the insulation itself but also for the overall health and safety of a building's occupants. The insulated cavities of walls can unfortunately provide an ideal environment for various pests, such as rodents, insects, and birds, to nest and thrive. Rodents, such as mice and rats, are particularly problematic. They can easily find their way into the cavity walls and once inside, they can cause substantial damage. These pests have a tendency to gnaw on insulation materials, reducing their effectiveness. Moreover, rodents can chew through electrical wiring, posing serious fire hazards. Their nesting and breeding within the insulation can also lead to unpleasant odours and potential health risks, as rodent droppings and urine contribute to unsanitary conditions. Insects, including ants and termites, can also infest cavity wall insulation. Termites, in particular, are known for their destructive capabilities, especially with certain types of insulation materials that may provide a food source or habitat. The presence of these insects can go unnoticed for long periods, allowing them to cause extensive damage not only to the insulation but also to the structural elements of the building. Birds nesting in cavity walls is another concern. While not as destructive as rodents or insects, birds can displace insulation materials, creating gaps and reducing the insulation's effectiveness. Their nests can block ventilation openings, leading to problems with dampness and reduced air quality.
The alternative - external wall insulation
Our favoured alternative to cavity wall insulation is external wall insulation. This involves the installation of a whole insulating envelope to the external facade. The benefits extend far beyond energy efficiency; external wall insulation can prevent condensation, provide acoustic insulation, and aid in refreshing your facade as decorative thin coat renders cover the surface. Moreover, these render systems provide ample durability and weatherproofing benefits.