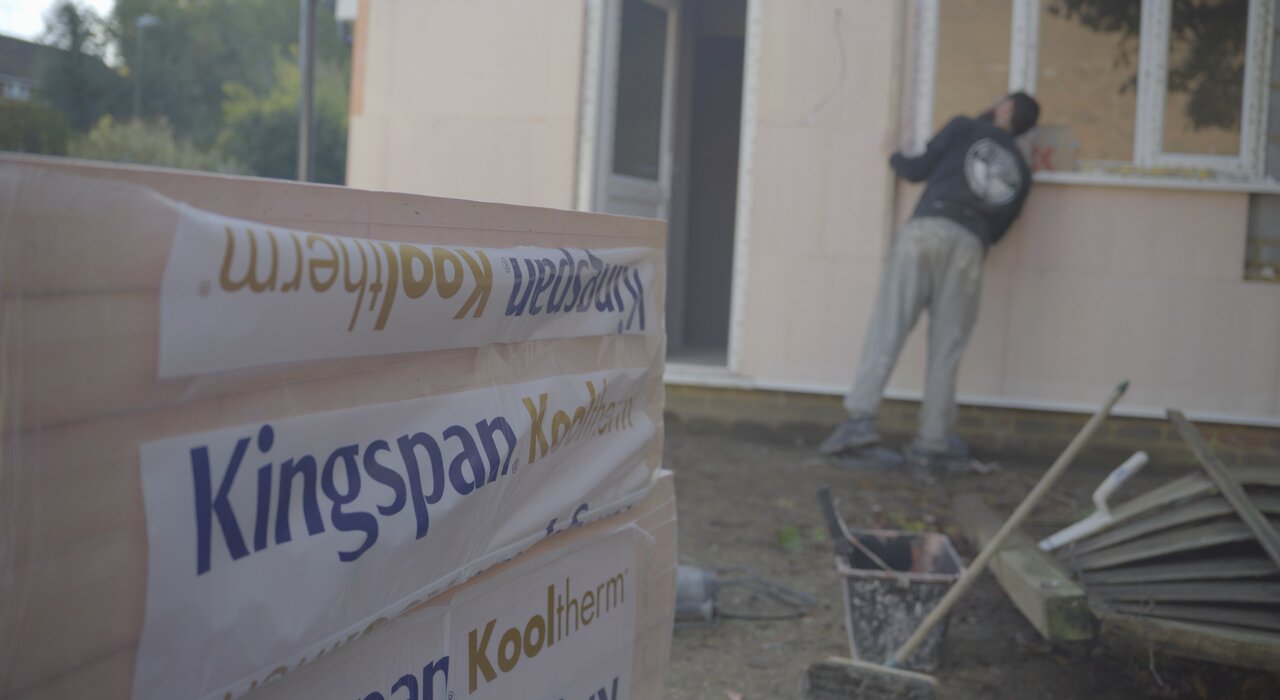
EWI provides a thermal comfort layer to your property. For this to persist, the durability and reliability of the system is crucial. Therefore, it is also crucial to understand what factors affect an EWI system. After installation of the EWI system, it must face many external factors that cause erosion and other types of damage. The system is directly exposed to thermal effects, frost corrosion, wind effects, thermal deformation, biological corrosion, soiling of the entire or parts of the facade, static and dynamic deformation of the structure, and mechanical damage - operational or acts of vandalism.
EWI system installation
Correct installation will invariably play a part in the overall durability and reliability of the system. The durability of the EWI system is determined by various factors. These include the proper preparation of the substrate and its condition, correct execution, and ongoing maintenance.
The substrate must be smooth, clean, dry, and well-bonded. It must also be free of deposits, efflorescence, greasy stains, or other substances that impede adhesion. Additionally, the substrate must be even, and any unevenness greater than allowed by the system manufacturer must be compensated for by the thickness of the thermal insulation material, not by additional thicknesses of the adhesive mortar. It is also essential that the substrate, apart from the proper levelling and preparation, must be static and load-bearing.
The EWI system attached to such a substrate must be well bonded to the substrate using an adhesive mortar. Mechanical fixings are also recommended. Therefore, it is worth having a professional verification of the strength of such a substrate for tearing and the strength of mounting connectors in such a substrate, especially in the case of existing objects.
The proper execution stage is another element that affects durability. In this case, it is essential to strictly follow the technological regime including gaps between work. Also, be mindful to carry out work in suitable weather conditions. Such requirements are always presented by the manufacturer of a given EWI system.
The final factor determining durability is the proper operation of the system. Therefore, carrying out mandatory annual inspections of the technical condition of the facade is crucial. Failure to carry out minor repairs during the use of the object may result in its operational durability and properties.
Factors affecting durability and reliability
Thermal effects
Thermal effects refer to the impact of temperature changes on a material or structure. Fluctuating temperatures can cause expansion and contraction, which can lead to fatigue, cracking, and reduced overall durability. Materials with low thermal conductivity or high coefficients of thermal expansion are more susceptible to thermal stress, potentially reducing their reliability over time.
Frost corrosion
Frost corrosion is a phenomenon where freezing temperatures cause moisture to seep into the pores of materials, such as concrete or metals. Upon freezing, the water expands, creating internal stress within the material. This can cause cracks and corrosion, ultimately leading to a decline in structural integrity and durability.
Wind effects
Wind effects on structures and materials include the forces exerted by gusts and sustained winds, as well as vibration and buffeting. These forces can cause stress on connections, joints, and the overall structure, leading to fatigue and damage over time. Sustained exposure to wind can also lead to corrosion, especially in coastal areas where salt-laden air contributes to the deterioration of materials.
Thermal deformation
Thermal deformation is the distortion or warping of a material due to changes in temperature. It occurs when different parts of a structure or material expand or contract at different rates, creating stress and causing permanent deformation. This can result in a reduction in the material's strength and overall reliability, and in severe cases, can lead to structural failure.
Biological corrosion
Biological corrosion refers to the degradation of materials caused by the growth of microorganisms, such as bacteria, fungi, or algae. These organisms can produce acids or enzymes that break down materials, leading to corrosion and weakening of the structure. This type of corrosion is particularly prevalent in warm, humid environments and can significantly impact the durability and reliability of materials. Nano Drex Silicone Render and Premium Bio Silicone Render are specially designed to actively resist and break down biological growth. Nano Drex particles are additives that affect the chemical and biological formation of microorganisms, preventing them from settling.
Soiling
Soiling refers to the accumulation of dirt, dust, and other contaminants on a material or structure. It can be either partial or total; the most frequent occurrence of soiling or staining is on the building plinth as water and dirt can splash back from the floor. These substances can cause physical and chemical changes to the surface, reducing its resistance to wear, corrosion, and other forms of damage. Soiling can also impact the performance of certain materials, such as solar panels, by reducing their efficiency and shortening their lifespan.
Static and dynamic deformation
Static deformation refers to the change in shape or size of a material or structure under constant load, while dynamic deformation refers to changes that occur as a result of fluctuating loads, such as those from wind, earthquakes, or vibrations. Both types of deformation can lead to fatigue, cracking, and a reduction in the material's strength and reliability over time.
Mechanical damage
Mechanical damage encompasses any physical damage caused to a material or structure by external forces or impacts. This can include scratches, dents, gouges, and abrasions, as well as more significant damage from accidents or extreme weather events. Mechanical damage can weaken materials, reducing their durability and reliability, and making them more susceptible to other forms of degradation.
How EWI Store products enhance durability & reliability
EWI system products will inherently have some compressive strength. However, certain products have enhanced capabilities when it comes to durability. For example, Kingspan K5 insulation boards have much higher compressive strength. As such, they are far more suitable for areas that may be susceptible to some form of mechanical impact. This may include narrow passages and most urban areas. Silicone render is innately strengthened by the presence of silicone fibres. Therefore, it can resist mechanical impact, vandalism, or accidental and incidental impact. This includes something minor like a ball being kicked against the wall. EWI systems also include Fibreglass Mesh which strengthens the system.