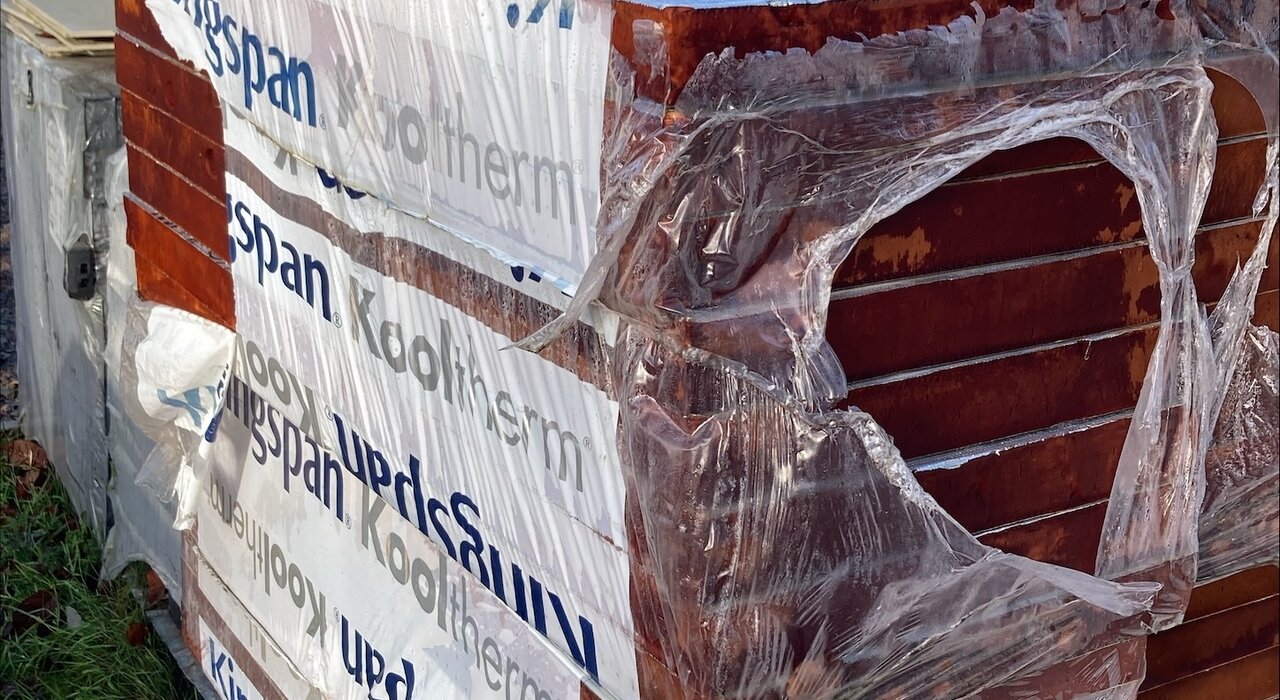
- Relying on solely mechanical fixings or adhesives
- Mistake
- Fix
- Filling gaps with basecoat
- Mistake
- Fix
- Incorrect sealing of verge trims
- Mistake
- Fix
- Omitting beading
- Mistake
- Fix
- Not overlapping fibreglass mesh by 100mm
- Mistake
- Fix
- Diluting your silicone render
- Mistake
- Fix
- Inadequate storage and protection for products on-site
- Mistake
- Fix
- Incorrect boarding patterns
- Mistake
- Fix
EWI systems offer a fantastic way to improve the thermal performance of a building, reduce energy consumption, and enhance the exterior appearance. However, the installation process is fraught with potential pitfalls that can compromise the effectiveness and longevity of the system. Let's explore some common EWI mistakes and provide practical advice on how to fix them, ensuring a successful installation.
Relying on solely mechanical fixings or adhesives
Mistake
One of the most common misconceptions in EWI installations is the belief that mechanical fixings or adhesives alone are sufficient to secure insulation boards to the exterior walls. This approach can lead to significant issues down the line. For instance, relying solely on mechanical fixings might result in a lack of full surface adhesion. This can cause air pockets between the insulation and the wall. These air pockets can drastically reduce the insulation's effectiveness. On the other hand, using only adhesive might compromise the long-term security of the system, especially in areas exposed to high wind loads or extreme weather conditions. Ultimately, this leads to potential detachment or failure of the insulation boards.
Fix
The optimal approach to securing EWI boards is a combination of both adhesive and mechanical fixings.
- Adhesive Application: Begin by applying a continuous bead of adhesive around the perimeter of the back side of each insulation board, about 5cm from the edges. Then, add dabs of adhesive (about the size of a palm) evenly across the centre area. This method ensures complete surface contact and immediate adhesion to the wall, effectively reducing thermal bridging by eliminating air gaps.
- Mechanical Fixings: After the adhesive, mechanical fixings should be applied. These provide additional security and ensure the insulation boards are firmly anchored to the wall. The number of fixings required will depend on the insulation material, board size, and the specific conditions of the building site, such as exposure to wind. Generally, fixings should be placed at the corners of each board and in the centre. The typical density is five fixings per square meter. Selecting the appropriate length and fixing the substrate and insulation material is crucial for optimal performance.
Filling gaps with basecoat
Mistake
A standard error during the installation of EWI systems is filling gaps between insulation boards with basecoat instead of using offcuts of the same insulation material. This mistake arises from a misunderstanding of the basecoat's role and properties. The basecoat is designed to provide a solid, smooth surface for the render finish and to embed the reinforcing mesh, not to act as an insulating material. When gaps between insulation boards are filled with basecoat, it creates thermal bridges. A thermal bridge is an area where heat can transfer faster than through the insulation. This undermines the insulation's effectiveness, increasing energy consumption and heating or cooling costs.
Fix
To maintain the thermal continuity of the EWI system and ensure its effectiveness, filling any gaps between insulation boards with offcuts of the same insulation material is crucial. Here's the correct approach:
- Measure and Cut Offcuts Precisely: When you encounter gaps between insulation boards, measure the gap size accurately. Use offcuts of the cut insulation material to fit these measurements exactly. It's crucial to ensure a snug fit to prevent thermal bridging.
- Apply Adhesive to Offcuts: Apply adhesive to the sides of the offcuts, similar to how you would install a full-size insulation board. This ensures that the offcuts are securely bonded to the primary insulation boards and the wall, providing continuous insulation coverage.
- Smooth Out Joints: After the offcuts are in place, ensure the surface is levelled with the surrounding insulation boards. Any surface-level discrepancies can be gently sanded down once the adhesive has set, but do not compromise the insulation's integrity.
- Check for Gaps: Once all boards and offcuts are installed, inspect the entire surface for any remaining gaps, no matter how small. Even tiny gaps can significantly impact the system's overall thermal performance. Fill these with appropriate insulation materials.
Incorrect sealing of verge trims
Mistake
A frequent oversight in EWI installations is the improper sealing of verge trims. Verge trims are critical components that protect the edges of the insulation system, particularly around roofs and wall edges, from weather elements. The mistake often made is using silicone sealant as the sole barrier against moisture without incorporating a secondary membrane. Relying solely on silicone sealant can lead to vulnerabilities in the system. Silicone may degrade over time due to exposure to UV light, temperature fluctuations, and physical wear. This degradation can form gaps, allowing water ingress to damage the insulation material and the underlying structure.
Fix
To ensure a durable and weatherproof seal around verge trims, a two-step approach should be adopted:
- Install a Secondary Membrane: Before applying any sealant, it's essential to install a secondary, breathable yet waterproof membrane around the edges where the verge trims will be placed. This membrane acts as an additional layer of protection, helping to divert water away from the insulation system and the structure of the building. The membrane should be carefully measured, cut, and securely fixed to overlap with the wall insulation, providing a continuous barrier against moisture.
- Apply Silicone Sealant: Once the secondary membrane is in place, silicone sealant can then be applied to seal the edges of the verge trims. The sealant should be applied evenly and thoroughly, ensuring no gaps or holes through which water can enter. Selecting a high-quality, exterior-grade silicone sealant compatible with the membrane and materials used in the EWI system is essential.
Omitting beading
Mistake
Omitting beading from EWI systems is a significant oversight that can compromise the insulation project's aesthetic and structural integrity. Beading is crucial in creating clean, defined edges around windows, doors, and corners and reinforcing areas prone to impact or stress. Without beading, these areas are more susceptible to cracking, chipping, and uneven finishes, detracting from the facade's overall appearance and reducing the insulation's effectiveness.
Fix
Incorporating beading into an EWI system is essential for ensuring durability, aesthetic appeal, and optimal performance.
- Selection of Appropriate Beading: Choose the correct type of beading for each specific application. For example, corner beads reinforce external corners, while movement beads are used in areas susceptible to expansion and contraction. Ensure the beading material matches the EWI system components and intended finish.
- Installation at Key Points: Beading should be installed around all windows, doors, and other openings, along with corners and any areas that require additional structural reinforcement. The placement of beading should be carefully planned to align with the design and architectural features of the building.
- Secure Fixing: Beading should be securely fixed into place using the appropriate adhesive or basecoat recommended by the EWI system manufacturer. The adhesive or basecoat should be applied under and over the beading to ensure it is fully embedded within the system. This secures the beading and provides a smooth surface for the finish coat.
- Alignment and Leveling: It's crucial to ensure that all beading is straight and level before the adhesive or basecoat sets. Misaligned beading can lead to aesthetic issues and may affect the performance of the EWI system. Use a spirit level and measuring tools to check alignment during installation.
- Finishing: Additional coats can be applied once the beading is installed and the basecoat has cured. The beading should be covered entirely, with the finish coat extending slightly beyond the edge of the beading to ensure a seamless appearance.
Not overlapping fibreglass mesh by 100mm
Mistake
A critical mistake in applying EWI systems is failing to overlap fibreglass mesh within the basecoat layer. Fibreglass mesh is crucial, reinforcing the basecoat to prevent cracking, distributing stresses evenly, and enhancing the system's overall strength and durability. Without proper overlapping, the mesh fails to provide a continuous reinforcement layer, leading to weak points where cracks can quickly develop, especially in areas subjected to thermal expansion and contraction or physical impacts.
Fix
Correct overlapping of fibreglass mesh is essential to ensure the structural integrity and longevity of an EWI system.
- Measure and Cut the Mesh: Before applying the mesh to the basecoat, measure and cut it to allow for adequate overlap between sheets. The standard practice is to overlap the mesh by at least 10cm (about 4 inches) on all sides. This overlap ensures the mesh forms a continuous reinforcement layer across the surface.
- Apply the Basecoat in Sections: Work in manageable sections when applying the basecoat to ensure the mesh can be embedded before the coat starts to set. The basecoat should be applied evenly across the surface at the recommended thickness by the manufacturer.
- Embed the Mesh: Lay the first sheet of mesh onto the wet basecoat and gently press it into the surface with a trowel, ensuring no wrinkles or air pockets. The mesh should be fully embedded into the basecoat.
- Overlap the Mesh: When laying the next sheet of mesh, overlap it over the previous sheet by at least 10cm. Continue this process, ensuring each new piece of mesh overlaps the last pieces to create a continuous reinforcement layer. Pay special attention to corners and edges where additional reinforcement might be needed.
- Ensure Full Coverage: After all the mesh is applied, apply another thin layer of basecoat over the mesh to fully encapsulate it. This layer should be smooth and even, ready for the final finish coat once dried and cured.
Diluting your silicone render
Mistake
A widespread but critical error in applying EWI systems is the dilution of silicone render. Silicone render is a popular choice for the final coat due to its excellent water repellency, breathability, and flexibility, essential for the facade's long-term protection and aesthetic appeal. However, some installers dilute silicone render with water or other solvents. This dilution can severely compromise the render's inherent properties. This leads to reduced durability, diminished water resistance, and an overall decrease in the quality and appearance of the finish.
Fix
To ensure the optimal performance and longevity of silicone render in an EWI system, follow these detailed guidelines:
- Adhere to Manufacturer Specifications: Always follow the manufacturer's instructions regarding preparing and applying silicone render. These instructions ensure the render performs as intended, providing a durable, attractive finish that protects the building envelope.
- Do Not Dilute: Avoid the temptation to dilute silicone render. Adding water or any other substance can alter the chemical composition of the render, affecting its adhesion, texture, and protective qualities. Silicone render is formulated to be applied as is, without dilution.
- Proper Application Techniques: If the render seems too thick or challenging to apply, review your application techniques rather than altering the product. Use the correct tools, such as a stainless steel trowel or spray equipment recommended by the render manufacturer, and apply the render in thin, even coats. Ensure the basecoat is appropriately prepared, dry, and primed, if necessary, to facilitate the best application of the silicone render.
- Training and Practice: Ensure that installers are adequately trained and have sufficient practice in applying silicone render. Good technique is crucial for achieving a smooth, even finish. Manufacturers often provide training courses or detailed guides on using their products effectively.
- Temperature and Weather Conditions: Be mindful of the temperature and weather conditions during application. Extreme temperatures, direct sunlight, or high humidity can affect the render's consistency and drying time. Apply the render under conditions recommended by the manufacturer to avoid these issues.
Inadequate storage and protection for products on-site
Mistake
One of the common oversights during the installation of EWI systems is failing to protect materials and products on-site, especially in adverse weather conditions. Insulation materials, renders, and other components are sensitive to moisture, temperature extremes, and physical damage. When left exposed to the elements, these materials can suffer degradation that compromises their performance and the overall quality of the EWI installation. For example, moisture can affect the adhesive attributes of renders and basecoat. Moreover, direct sunlight can cause premature curing or warping of insulation boards.
Fix
Proper site management and protection strategies are essential to ensure that all materials retain their intended properties and are fit for use when needed.
- Cover and Elevate Materials: Ensure all insulation boards, renders, and other materials are stored off the ground and covered with waterproof sheeting. This protects them from ground moisture, standing water, and rain. Materials should also be shielded from direct sunlight, which can cause excessive heat buildup and damage or deformation.
- Secure Storage: Use safe, possibly ventilated storage solutions for sensitive components, such as adhesives and silicones, to protect them from temperature extremes and humidity. Store these materials in a controlled environment, especially during hot or cold weather.
- Careful Handling: Train site personnel in correctly handling and storing EWI materials to prevent physical damage. Insulation boards, for example, can be easily damaged on the edges and corners if mishandled.
- Weather Planning: Monitor weather forecasts and plan work schedules accordingly. Avoid leaving materials uncovered or outside storage areas for extended periods, especially if adverse weather is anticipated. Implementing a proactive approach to weather conditions can significantly reduce the risk of material damage.
- Use Protective Barriers: For materials that must remain outside, use sturdy protective barriers that can withstand wind and provide shade from direct sunlight. Ensure the protective coverings are secured against wind to prevent them from being blown away.
Incorrect boarding patterns
Mistake
Incorrect boarding patterns during the installation of EWI systems can significantly impact the durability and strength of the insulation layer. A common mistake is installing insulation boards in a straight line, one directly above the other. This creates vertical and horizontal seams that align across multiple layers. This alignment can compromise the structural integrity of the insulation, leading to potential weaknesses in the system. Additionally, failing to cut insulation boards in an L shape around windows and other openings can result in reduced insulation effectiveness and increased thermal bridging.
Fix
Proper boarding patterns and cutting techniques are crucial for enhancing the overall performance and durability of an EWI system.
- Stagger Boarding Patterns: Insulation boards should be installed in a staggered pattern, similar to brickwork, where one row's joints are offset from the rows above and below. This pattern distributes the load more evenly and helps to avoid the creation of straight-line weaknesses throughout the insulation layer. Staggering the joints also contributes to a more uniform distribution of adhesive and mechanical fixings, enhancing the system's overall stability.
- L-Shaped Cuts Around Openings: When insulating around windows, doors, and other openings, insulation boards should be cut in an L shape to fit snugly and maintain insulation continuity. This method reduces the needed cuts, thereby minimising thermal bridging around openings. It also provides a more aesthetically pleasing finish, ensuring the insulation layer looks continuous and uniform.
- Measure and Cut Precisely: Accurate measurement and cutting of insulation boards are vital in achieving a staggered pattern and proper L-shaped cuts around openings. Use appropriate tools, such as insulation saws or cutters, to make clean, straight cuts. Precise cutting ensures that the boards fit tightly together, reducing gaps and the need for excess filling materials.
- Check Alignment Regularly: During installation, regularly check the alignment and level of the boards. Any adjustments should be made before the adhesive sets.
- Seal and Finish Properly: Once the insulation boards are installed, seal gaps with appropriate insulation material. A layer of basecoat and mesh is then applied. This reinforces the insulation layer and provides a smooth surface for the final render.