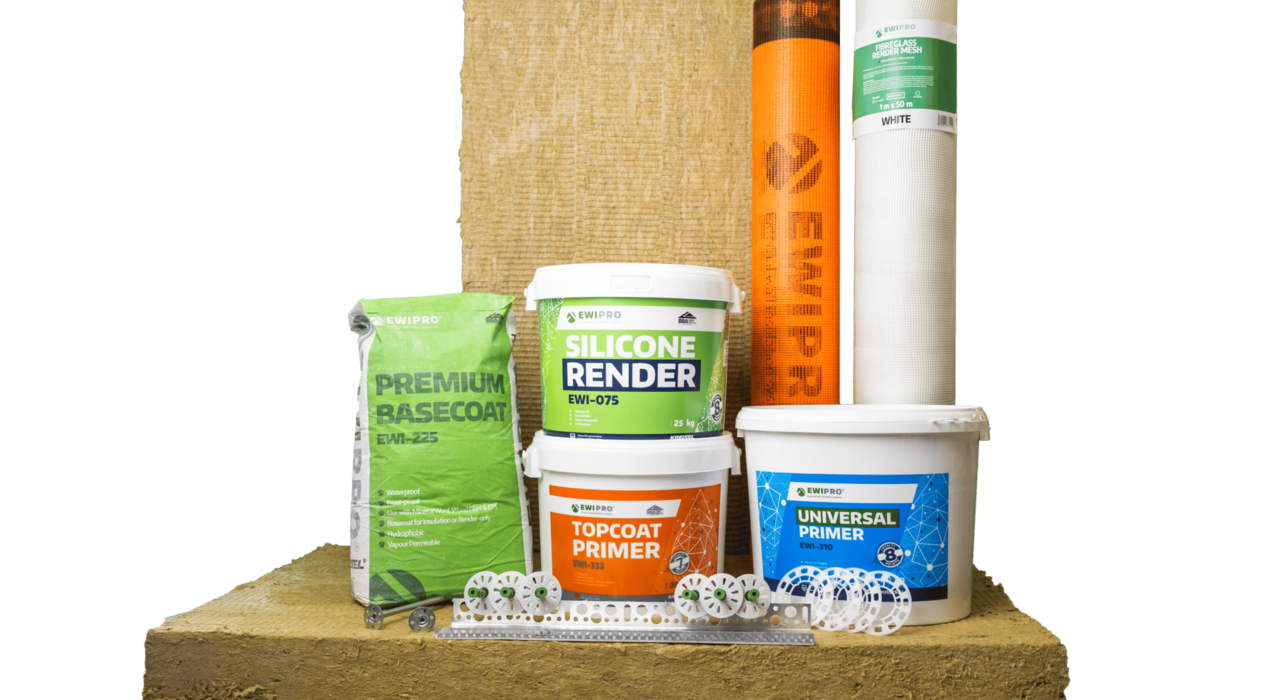
An External Wall Insulation system is a crucial element in promoting energy efficiency. The concept hinges on creating an uninterrupted thermal envelope. Therefore, every component in the EWI system has to work harmoniously to ensure there are no breaks in the envelope. At EWI Store, we provide the full range of materials required, from adhesive all the way to Swifix fixings. In today's blog, we will dissect how each component contributes to the system.
Why is an EWI system essential?
A continuous thermal envelope significantly improves the energy efficiency of a building. By providing a seamless layer of insulation, heat transfer between the interior and exterior of the building is reduced. This means less energy is needed to heat or cool the building, leading to lower energy bills and reduced greenhouse gas emissions. By regulating heat transfer, a well-insulated thermal envelope can maintain a more stable indoor temperature. This enhances the comfort levels inside the building, providing a consistently comfortable living or working environment, regardless of the weather conditions outside. An uninterrupted thermal envelope helps prevent thermal bridging, which occurs when heat bypasses the insulation through more conductive materials in the building envelope. Thermal bridges can significantly reduce a building's overall thermal performance. By ensuring the insulation is continuous, thermal bridging is minimised, and the insulation performs to its full potential. A continuous thermal envelope reduces the risk of condensation within the building's walls and roof. This is because it helps maintain the surface temperatures of these elements above the dew point of the interior air. Preventing condensation reduces the risk of dampness and mould growth, which can be harmful to both the building's and its occupants' health. With a well-sealed thermal envelope, there's less infiltration of outdoor air, which can often contain dust, allergens, pollutants, and even pests. Therefore, indoor air quality can be better controlled and maintained, contributing to healthier living and working conditions. An uninterrupted thermal envelope helps protect the building's structure from potential damage caused by moisture and temperature fluctuations, contributing to the building's long-term durability and reducing maintenance costs over time.
Substrate Primer
Substrate primer acts as a sealer and bonding agent for the EWI system. This compound is often water-based and designed to penetrate and seal porous substrates. Applying the primer helps ensure that the substrate doesn't absorb the moisture from the adhesive and compromises the bonding process. It also helps reduce dust and improves the adhesive's grip on the surface, creating a more secure base for subsequent layers.
Adhesive
The adhesive in an EWI system is typically a specially formulated compound that offers strong bonding properties and flexibility to cope with building movements. The adhesive can also fill small gaps and cracks in the existing wall, creating a smoother base for the insulation boards. In some EWI systems, the adhesive is also used for the initial basecoat, performing a dual function. Our 3 major basecoat adhesives are EWI225 Premium Basecoat, EWI-220 EPS Basecoat, and EWI-222p Performance Basecoat. All of these double up as basecoats and adhesives for certain insulation boards. As such, they are superior to single-purpose basecoats or adhesives, and crucially, contribute to less wastage on site.
Insulation Boards
Insulation boards are made from materials like expanded polystyrene (EPS), mineral wool, or phenolic foam, each offering unique insulating properties. They are cut to size and placed meticulously to ensure there are no gaps between them, contributing to a seamless thermal envelope. They serve as the primary layer of thermal resistance, significantly reducing heat transfer through the building's exterior walls. EPS, Mineral Wool, and phenolic foam all have different U-values, R-values, and lambda values. Depending on the substrate and the thickness of the insulation boards, they will produce different U-values. However, as per the UK's Building Regulations, retrofits need to achieve a U-value of 0.30 W/m²K. New builds need to achieve a U-value of 0.18 W/m²K, but modern building materials contribute to overall U-values therefore the thickness of the insulation remains similar to retrofits. The thickness required can be estimated through simple U-value calculations and results in the following requirements:
- EPS - 90mm
- Mineral Wool - 110mm
- Kingspan K5 (phenolic) - 60mm
Basecoat
The basecoat helps bind the insulation boards to the reinforcement layer (fibreglass mesh). This layer's thickness can vary depending on the system specifications, but it's typically applied to cover the insulation boards and the mechanical fixings entirely, creating a smooth and even surface for the final layers. Some basecoats are enhanced with water-resisting properties for additional protection against dampness. As aforementioned, many of our basecoats are dual-purpose, resulting in less wastage. They also contribute to enhanced impact resistance owing to the enhanced recipe developed by our sister company EWI Pro.
Fibreglass Mesh
Fibreglass mesh is a crucial element for an EWI system's longevity. The mesh is embedded into the wet basecoat, serving to reinforce and add strength to the system. It provides resistance to stress cracks and impacts that could potentially damage the insulation layer. Additionally, the mesh is flexible, allowing the system to withstand small shifts in the building structure without cracking.
Mechanical Fixings
Mechanical fixings, usually in the form of plastic or metal anchors, are used to add extra stability to the insulation boards. They are drilled through the insulation layer into the original wall substrate. Their role becomes especially important in tall buildings or areas exposed to high wind loads where the adhesive alone might not provide sufficient hold. As the fixings are fully embedded and often covered by dowel caps, they ensure that no thermal bridges are created. Thermal bridging is a persistent issue in buildings; any breaks in the thermal envelope act as 'heat highways' through which the heat inside the home travels to the colder areas outside.
Topcoat Primer
The topcoat primer serves as a bridge between the basecoat layer (with the embedded mesh) and the final render. This layer prepares the surface for the application of the topcoat by enhancing adhesion, equalizing absorption, and filling any remaining pores or minor imperfections. The outcome is a smoother and more consistent final appearance.
Silicone Render
As the final layer of the EWI system, silicone render serves both functional and aesthetic purposes. It's a type of topcoat known for its excellent water resistance and breathability, meaning it can repel rainwater while allowing water vapour from inside the building to escape. This prevents moisture buildup within the wall. Additionally, silicone render can be mixed with different pigments for a wide array of colours, offering a desirable finish that can be tailored to any aesthetic preference. Whilst Silicone Render has little value in terms of lowering U-values, the weather resistance it provides is crucial. Water ingress can cause structural issues but it also means that insulating materials work less efficiently and degrade.
SWIFIX Fixings
SWIFIX fixings are unique fixings used for securely attaching secondary items, like pipes, satellite dishes, or other fixtures to the insulated façade. These fixings are designed to avoid thermal bridging, meaning they won't compromise the insulation's effectiveness. They're installed through the insulation into the original wall substrate, forming a strong, thermally efficient fixing point that matches the EWI system's depth.