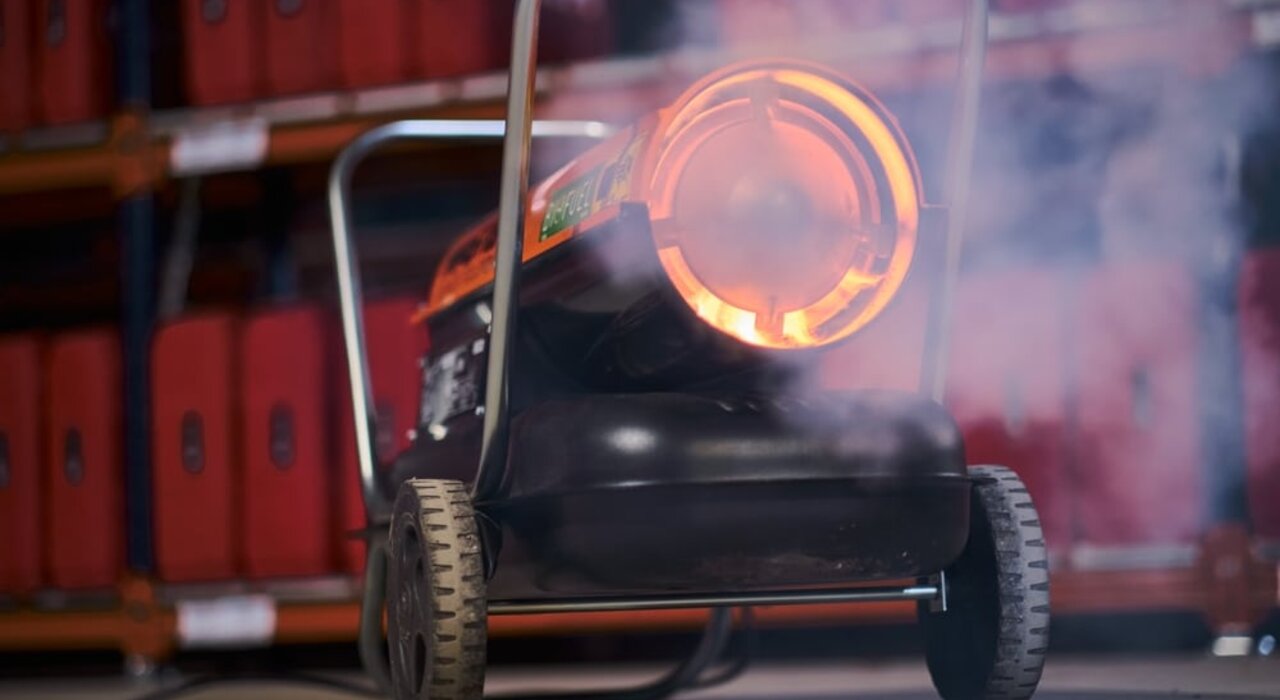
- The challenge of drying in cold and humid conditions
- Reduced Evaporation Rate in Cold Temperatures
- High Humidity Impedes Evaporation
- Condensation Risks
- Impact on Chemical Processes
- Practical Challenges
- Solutions to accelerate drying times
- Indirect Diesel-Fired Heaters
- Dry Air Electric Fan Heaters
- Using Render Accelerators
- Enhanced Air Circulation
- Dehumidifiers
- Environmental Control and Monitoring
- Scheduling and Planning
When working with basecoats and renders, managing drying times can be critical to your project's success, especially in challenging weather conditions. Understanding how to effectively accelerate these drying times in colder weather and higher humidity environments is essential for ensuring a smooth and efficient workflow.
The challenge of drying in cold and humid conditions
Drying basecoats and renders effectively is a straightforward process in ideal weather conditions, but it becomes significantly more challenging in cold and humid environments. The reasons behind this difficulty are rooted in the basic principles of evaporation and condensation.
Reduced Evaporation Rate in Cold Temperatures
Evaporation is the primary mechanism through which water in basecoats and renders dissipates. This process is heavily influenced by temperature. In cold conditions, the evaporation rate of water is drastically reduced. This is because the molecules in the water do not receive enough thermal energy to transform into vapour. As a result, the drying process is substantially slowed down in colder weather.
High Humidity Impedes Evaporation
Humidity refers to the amount of water vapour present in the air. In high humidity conditions, the air is already saturated with moisture. As such, leaving little room for additional water vapour from the wet render or basecoat. This saturation creates an equilibrium where the rate of water evaporating from the render is equal to the rate of moisture returning to the surface from the air. Consequently, the overall drying process is significantly slowed down.
Condensation Risks
There's also the risk of condensation in cold and humid conditions. When the temperature of the render or basecoat drops below the dew point of the surrounding air, moisture from the air can condense on the surface. This adds more moisture to the surface, further impeding the drying process.
Impact on Chemical Processes
Many renders and basecoats rely on certain chemical reactions to harden and cure. These reactions can be temperature-dependent. Cold weather can slow down or even inhibit these chemical processes, leading to longer drying times and potentially affecting the final strength and durability of the product.
Practical Challenges
Working in cold and humid conditions not only slows down the drying process but can also pose practical challenges for builders and decorators. It can lead to delays in work schedules and may require additional measures. These measures include heating or covering the work area, to ensure proper drying.
Solutions to accelerate drying times
To counteract the challenges posed by cold and humid conditions, various solutions can be implemented to accelerate the drying times of basecoats and renders. These solutions take into account the limitations of conventional gas heaters and focus on more effective alternatives like indirect diesel-fired heaters and dry air electric fan heaters. Heaters blow out warm dry air which naturally helps with evaporation. However, being blow heaters as opposed to radiant, they also circulate air. Air circulation is another crucial part of the equation.
Indirect Diesel-Fired Heaters
Indirect diesel-fired heaters are highly efficient for heating large spaces and are particularly suitable for construction sites. Unlike direct heaters, they expel combustion gases outside, ensuring that only clean, dry heat is circulated within the work area. This type of heater is ideal for maintaining a consistent and controllable temperature, thus enhancing the drying process without introducing additional moisture or harmful fumes into the environment. Due to the combustion being contained, these units can be ducted into the work area.
Dry Air Electric Fan Heaters
These heaters are another excellent option for accelerating drying times. They work by circulating dry, warm air throughout the space, which helps in reducing humidity and increasing the evaporation rate of the moisture in the renders or basecoats. Being electric, they do not produce combustion gases, making them safer and more suitable for enclosed or poorly ventilated spaces. Many large electric heaters can also be ducted into areas where space is at a premium.
[caption id="attachment_70053" align="aligncenter" width="300"] Electric fan heater to accelerate drying (El Bjorn)[/caption]
Using Render Accelerators
Adding render accelerators to the mix can significantly reduce the time it takes for the render to set and dry. These additives are designed to speed up the chemical reactions necessary for curing, thus lessening the impact of cold weather on these processes.Enhanced Air Circulation
Implementing strong air circulation strategies, such as using high-capacity fans, can greatly assist in the drying process. Moving air helps to carry away the moisture-laden air from the surface of the renders, replacing it with drier air which can absorb more moisture.
Dehumidifiers
In conditions of high humidity, using dehumidifiers can be very effective. These devices help to lower the humidity level in the environment by removing excess moisture from the air, creating conditions more conducive to faster drying. A popular tactic for combatting indoor humidity is to pair indirectly fired diesel heaters with dehumidifiers. As the air provided by the heaters is dry and clean the heaters are safe to use indoors. Therefore, they are able to effectively aid with evaporation which is then extracted from the air by dehumidifers. Moreover, the combustion is also contained within the heater as opposed to being exposed.
Environmental Control and Monitoring
Creating a controlled environment using tarps or temporary enclosures can protect the work area from external weather conditions. Monitoring tools like hygrometers and thermometers can be used to keep a close watch on temperature and humidity levels, allowing for adjustments as necessary to maintain optimal drying conditions.
Scheduling and Planning
Timing the application of renders and basecoats during the warmer and drier parts of the day. Even postponing work to more suitable weather conditions can make a significant difference. This requires careful planning and flexibility in the work schedule.