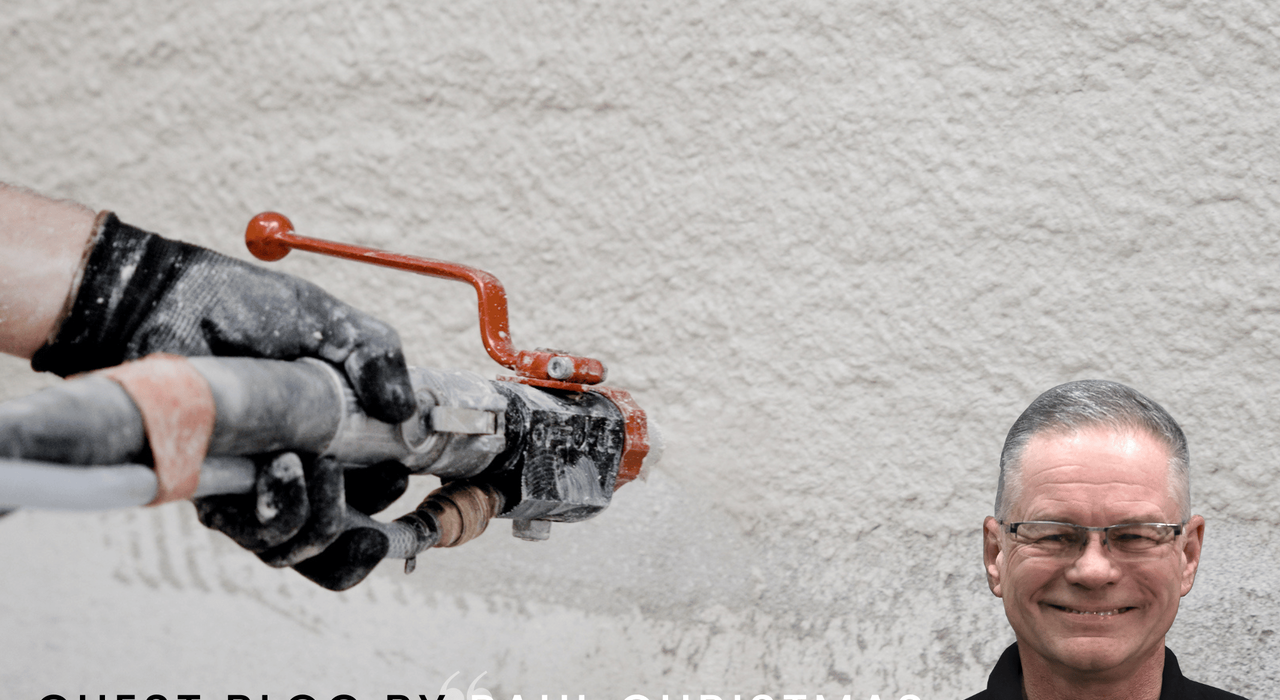
Table of contents
Technology has brought the process of rendering a long way; render spray machines cover entire walls in a matter of minutes. The skills required are very much on par with the skills required for applying render the old fashioned way. But what is the old fashioned way?
History of rendering
Rendering as a form of house plastering is thousands of years old. Evidence points to the practice being present throughout antiquity, even to the Pre-Roman days. The Roman form of rendering is remarkably similar to the modern form. Romans mixed lime, sand, gypsum, and marble dust, forming a mixture subsequently applied to walls. As a result, the surface was smooth and ideal for decorative frescos and paintings. In medieval Europe, a mixture of sand, clay, and straw coated external walls to provide a weather-resistant envelope. Even Leonardo da Vinci plastered the walls of the Sistine Chapel in a base relief, which gives the walls a 3D effect. The smooth finish provided the perfect base for the painting of his Renaissance masterpieces.
In the 19th century, the Industrial Revolution brought advances in building technology, including the production of Portland cement, which revolutionized the render industry. This allowed for the creation of stronger, more durable render that could withstand the harsh weather conditions of industrial cities.
So where does that place rendering today? And how did we get to the stage of developing render spray machines?
Rendering without spray machines
Rendering refers to the application of some form of cement-based substance to an external or internal wall. The objective can vary, but the aim is usually to provide a smooth surface. However, some renders will provide a textured finish, and many come in different grain sizes. The rendering process uses any of the following types of render:
- Silicone Render - Polymer modified and comes readily used. The silicone particles in this render give it greater flexibility and resistance to heat. EWI Pro's Silicone Render range is hydrophobic and breathable, which means it is the ideal topcoat for any external wall insulation system.
- Monocouche Scratch Render - Cement-based render renowned for its natural stone-like appearance. The Monocouche Scratch Render in EWI Pro's range offers increased flexibility and water-repellence whilst retaining the low-maintenance exterior.
- Cement Render - More of an overarching category encompassing most renders composed of sand, water, and additives. The additives distinguish the renders, giving them other benefits.
- Acrylic Render - Acrylic particles provide extra resistance to mechanical impact. EWI Pro's Acrylic Render is also water-repelling and frost-resistant, and offers excellent performance at an agreeable price point.
- Lime Render - Lime render tends to be particularly useful for repairs and retrofits of older, traditionally built stone buildings.
- Mineral Render - A quick-drying render, designed to be sealed with Silicone Paint to provide the same weatherproof benefits that Silicone Renders do.
The process
The process of applying render the old fashioned way as opposed to with a render spray machine varies on the type of render. Silicone Renders are sometimes referred to as thin-coat renders, and they only require one pass. Monocouche Renders require two passes (despite the name, French in origin, which describes the product as one pass). The traditional method relies on the skill of the applicator, and the tools used most often are a hawk and trowel.
- Silicone Render application - EWI Pro Silicone Render is ready-to-use and does not require water. The product should be mixed with a paddle mixer prior to application, and the surface should be cleaned prior to application. A trowel is used for the initial application of the render, to the same depth as the grain size the render comes in. However, Silicone Render must be applied on top of a basecoat layer, not directly onto a wall or insulation board. Rubbing the render with a plastic float achieves the desired texture.
- Monocouche Render application - Apply render to the primed surface in two passes. Apply the first pass with a stainless steel trowel or spray pump at a thickness of 10mm and embed fibreglass mesh in the first pass. Then, apply the second pass to a thickness of 8-9mm, then scratch it back to 2-3mm to give the completed finish. The total depth will be between 15-17mm. Drying time varies depending on weather conditions.
Rendering with a spray machine
A render spray machine has the capability to process and apply a large amount of render in a small amount of time. The machine, depending on the size and type, can handle pre-mixed materials, or even mix them inside the machine. Smaller machines would tend to require any material to be pre-mixed and then poured into the hopper before being dispensed.
As with trowel rendering, the surface needs to be clean and dust free. Once the nozzle and hose are adjusted, the operative should work consistently and in a snaking pattern. This will blend the render. Firstly, open the spray gun nozzle into a bucket; there will be an initial burst of air that you do not want on the wall, then transfer the gun onto the wall. As a result, the coverage will be consistent. Following the application of the render, you should use a trowel or a speed-skim to even out the surface. If the material you are applying is an adhesive, a notched speed-skim will create the required surface.
The benefits of using a spray machine over trowel rendering
As discussed previously, training is required to operate spray machines. They are complex instruments with several moving parts, and without proper instructions, can cause injury. Not to mention, you could end up with incorrectly mixed products and poor application.
The most obvious benefit of using a render spray machine is the speed at which you can work. Time can often be heavily limited on sites, especially in colder temperatures. A render spray machine can allow you to cover large parts of the wall. The process of operating the machine is also far less taxing than traditional rendering techniques.
The spray machines offered at EWI Store have also been extensively tested for compatibility. Therefore, you can actually apply the adhesive and basecoat layers with the same spray machine. This is the case for almost all of the EWI Store Basecoat range. As aforementioned, some machines are even capable of mixing render internally, which cuts down the time even further.
However, traditional rendering does retain a trump card on the spray rendering process. Spray rendering machines are not as subtle as hand-applied render, therefore any fascia, soffits, and gutters may need to be removed before the render is applied.
EWI Store's machines
EWI Store stocks two spray machines, offering fantastic flexibility for the customer. The Euromair DropPro 8P is a lightweight grout pump and rendering machine. The unit is a great product for smaller site work and spraying the following products:
- Thin-coat renders
- Plasters
- Lightweight renders
- Basecoats and adhesives
The larger 70L tank version of the Euromair range is the MixPro 28, and can cope with pumping floor screeds, as well as various plasters and renders. The major benefit of this unit is the compactable nature of it; it can be dismantled into four parts and as a result, fits easily into the back of a van. The MixPro28 is also a continuous mixing pump. The hopper can be filled with dry product as the unit has an internal water pump. The water pump, once primed and turned on, flows into the upper chamber, at which point, dry product is added. The machine then proceeds to knead and mix the product to produce a homogenous substance. The consistency can also be regulated with an adjustment hose.
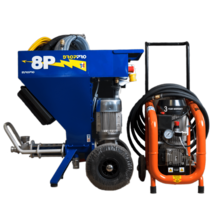