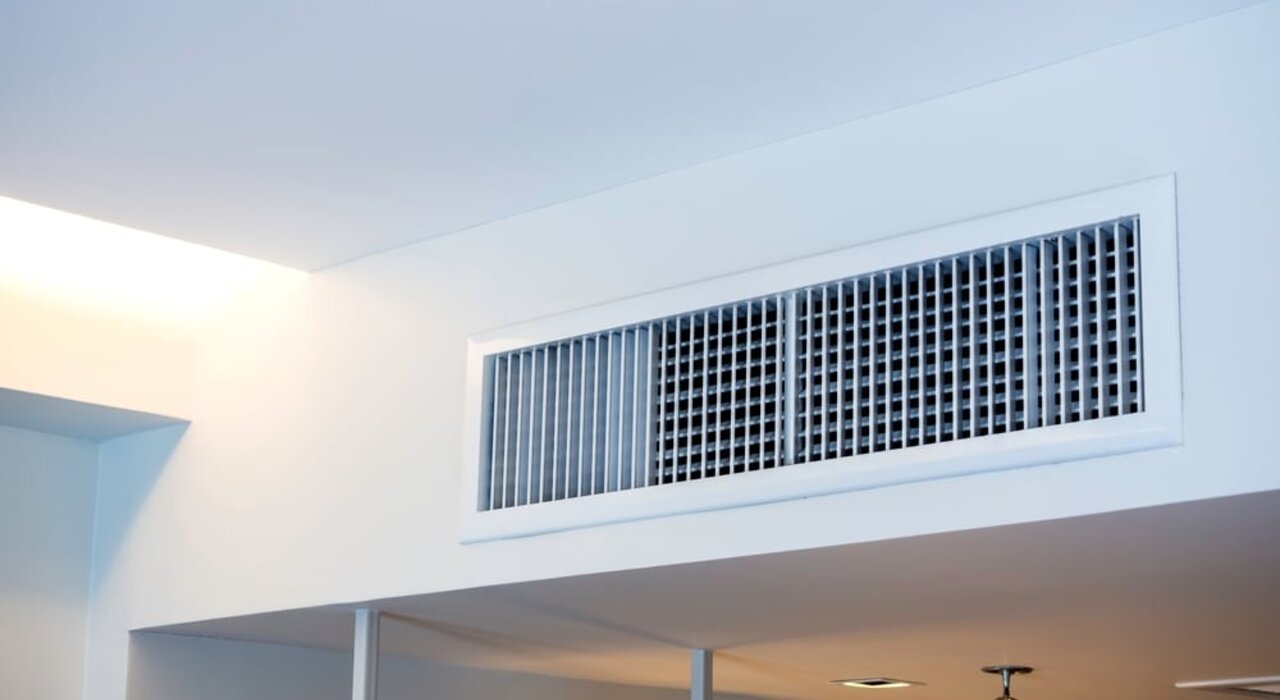
- Understanding the importance of ventilation in retrofits
- Preventing moisture build-up
- Maintaining indoor air quality
- Enhancing energy efficiency
- Preventing structural damage
- Compliance with building regulations
- Best practices for ensuring good ventilation
- Use breathable materials
- Install mechanical ventilation
- Ensuring natural ventilation is not compromised
- Strategies for Ensuring Natural Ventilation
- Airtightness and UK Building Regulations
Ventilation, in its essence, refers to the process of exchanging indoor air with outdoor air. This exchange is crucial for maintaining a healthy and comfortable indoor environment, especially in buildings undergoing retrofitting. When we talk about ventilation in the context of retrofits, especially those involving external wall insulation and silicone render, we are referring to a carefully designed system that balances the need for energy efficiency with the necessity of maintaining good air quality. The process of ventilation can be natural, mechanical, or a combination of both. Natural ventilation relies on passive airflow through windows, doors, and vents. Mechanical ventilation, on the other hand, uses fans and duct systems to remove stale air and bring in fresh air from the outside. In the context of retrofits with external wall insulation and silicone render, the choice of ventilation method becomes critical. These retrofit methods improve the building's thermal envelope, making it more energy-efficient but potentially less breathable.
Understanding the importance of ventilation in retrofits
Preventing moisture build-up
One of the primary reasons for ensuring proper ventilation in retrofits is to prevent the accumulation of moisture. External wall insulation and silicone render can significantly improve a building's thermal efficiency. However, they can also create a seal that traps moisture. This moisture, if not properly managed, can lead to dampness and mould growth, which not only damages the building structure but also poses health risks.
Maintaining indoor air quality
Indoor air quality is another critical factor. A well-insulated and rendered building is more airtight, which is excellent for energy efficiency but can lead to stale air and the accumulation of indoor pollutants. Adequate ventilation helps in exchanging indoor air with fresh outdoor air, thereby reducing the concentration of harmful pollutants and ensuring a healthier living environment.
Enhancing energy efficiency
While it may seem counterintuitive, proper ventilation can actually enhance the energy efficiency of a retrofitted building. By controlling the indoor air humidity and temperature, ventilation systems can reduce the load on heating and cooling systems, leading to energy savings in the long run.
Preventing structural damage
Inadequate ventilation can lead to an accumulation of condensation, particularly in colder months. This condensation can seep into the building's structure, leading to rot, corrosion, and other forms of structural damage. Ensuring good ventilation helps in mitigating these risks.
Compliance with building regulations
Building regulations often dictate specific ventilation requirements to ensure the safety and health of the occupants. In retrofits involving external wall insulation and silicone render, it's crucial to comply with these regulations to avoid legal complications and ensure the project's long-term success.
Best practices for ensuring good ventilation
Use breathable materials
Breathable materials in construction are those that allow water vapour to pass through them without letting water in. This ability to 'breathe' helps regulate moisture levels within the building structure. Common breathable materials include certain types of wood, bricks, and specific insulation materials like mineral wool or cellulose. When retrofitting with external wall insulation, it’s crucial to choose insulation materials that allow for moisture transmission. This is because the insulation layer can trap moisture, leading to potential dampness issues. Silicone render, known for its breathable properties, complements these insulation materials well. It provides a finish that allows moisture from inside the building to escape, thereby reducing the risk of condensation and mould growth. The breathability of these materials plays a critical role in regulating moisture levels. In a retrofitted building, daily activities like cooking and showering can produce significant amounts of moisture. Breathable materials help in wicking away this moisture, maintaining a dry and healthy interior environment. Over time, trapped moisture can cause significant damage to a building’s structure, such as rot in wooden elements or corrosion in metal components. Breathable materials help in mitigating these risks by allowing moisture to escape, thereby protecting the structural integrity of the building. By allowing for natural moisture regulation, breathable materials also contribute to better indoor air quality. They reduce the likelihood of mould and mildew development, which are known to cause health issues, particularly in people with respiratory problems. Interestingly, breathable materials can also contribute to energy efficiency. They help maintain a stable indoor climate, reducing the need for excessive heating or cooling. This stability can lead to lower energy consumption and, consequently, lower utility bills.
Install mechanical ventilation
Mechanical ventilation refers to systems that use mechanical means, like fans and ducts, to move air in and out of a building. Unlike natural ventilation, which relies on passive airflow, mechanical systems provide controlled and consistent air exchange regardless of external conditions. The types of mechanical ventilation systems are as follows:
- Exhaust Ventilation Systems: These systems remove air from inside the building to the outside, reducing indoor pollutants and moisture.
- Supply Ventilation Systems: These systems bring in fresh air from the outside, improving indoor air quality.
- Balanced Ventilation Systems: These systems combine both supply and exhaust, maintaining a balanced air pressure within the building.
- Heat Recovery Ventilators (HRV) and Energy Recovery Ventilators (ERV): These advanced systems not only balance the air exchange but also recover heat (and sometimes moisture) from the outgoing air to pre-heat or pre-cool the incoming air, enhancing energy efficiency.
Buildings with external wall insulation and silicone render are more airtight, which can lead to reduced natural air circulation. Mechanical ventilation systems ensure that fresh air is consistently introduced, and stale, humid air is extracted, thus preventing issues like mould growth and poor indoor air quality. While mechanical ventilation systems consume energy, their overall impact on a building’s energy efficiency can be positive. Systems like HRVs and ERVs minimise heat loss while ventilating, aligning with the energy-saving goals of the retrofit. Consistent air quality and moisture levels are crucial for occupant health and comfort. Mechanical ventilation ensures that these parameters are maintained, especially in regions with extreme climates where opening windows frequently may not be feasible.
Ensuring natural ventilation is not compromised
Natural ventilation is the process of supplying and removing air through natural means. It's achieved through the use of windows, doors, vents, and other openings, utilising natural forces like wind and thermal buoyancy. The benefits of natural ventilation when it comes to retrofits include:
- Air Quality: Natural ventilation helps in exchanging indoor air with fresh outdoor air, thereby reducing pollutants and stale air.
- Moisture Control: It aids in managing indoor humidity levels, crucial in preventing condensation and mould growth, especially in well-insulated buildings.
- Energy Efficiency: Natural ventilation can reduce the reliance on mechanical heating, cooling, and ventilation systems, thereby saving energy.
- Occupant Comfort and Well-being: Fresh air and natural light have been linked to improved mood and productivity, enhancing the overall well-being of occupants.
Retrofits that significantly improve airtightness, such as those with external wall insulation and silicone render, can restrict natural airflow. Thus, it’s vital to plan for adequate natural ventilation to prevent the building from becoming too sealed.
Strategies for Ensuring Natural Ventilation
- Window Design and Placement
- Operable Windows: Ensure that a portion of the windows in the building is operable to allow for airflow.
- Placement: Windows should be strategically placed to facilitate cross-ventilation. This involves positioning windows on opposite or adjacent walls to enable air to flow through the building.
- Use of Vents and Air Bricks
- Installing vents and air bricks can help in maintaining air circulation, especially in areas where windows cannot be frequently opened, like bathrooms and kitchens.
- Building Orientation and Design
- The building’s orientation can be optimised to take advantage of prevailing winds. Additionally, incorporating design features like courtyards or atriums can enhance natural air movement.
- Landscaping for Ventilation
- Thoughtful landscaping can direct natural breezes towards the building and can also act as a buffer against strong winds.
- Controlled Opening and Closing
- Educating occupants on the importance of opening windows regularly, especially in peak times like early mornings or late evenings, can significantly improve air quality.
- Combining with Mechanical Ventilation
- In some scenarios, a combination of natural and mechanical ventilation might be necessary to achieve optimal air quality and energy efficiency.
[caption id="attachment_70207" align="aligncenter" width="1000"] Wind towers are an ancient technique to promote natural ventilation[/caption]
Airtightness and UK Building Regulations
In the United Kingdom, building regulations have set specific standards for airtightness to ensure energy efficiency and comfort in buildings. These regulations are part of a broader effort to reduce energy consumption and carbon emissions in the built environment. The airtightness standard is measured in terms of air changes per hour (ACH) at a given pressure, typically 50 Pascals. The UK regulations for residential buildings, as specified in Part L of the Building Regulations, require an airtightness level of no more than 10 m³/h·m² at 50 Pa. This standard is critical in preventing excessive heat loss and ensuring energy efficiency. In contrast, the Passivhaus standard, originating from Germany and now widely recognised globally, sets a much more stringent criterion for air tightness. For a building to be certified as a Passivhaus, it must not exceed 0.6 air changes per hour at 50 Pascals. This rigorous standard is part of the Passivhaus concept, which aims to create buildings that are highly energy-efficient, comfortable, and sustainable. Achieving such a level of airtightness requires meticulous design and construction practices, including the use of high-performance insulation, windows, and ventilation systems. The significant difference in airtightness requirements between the UK building regulations and the Passivhaus standard highlights the varying approaches to energy efficiency and sustainability in building design.