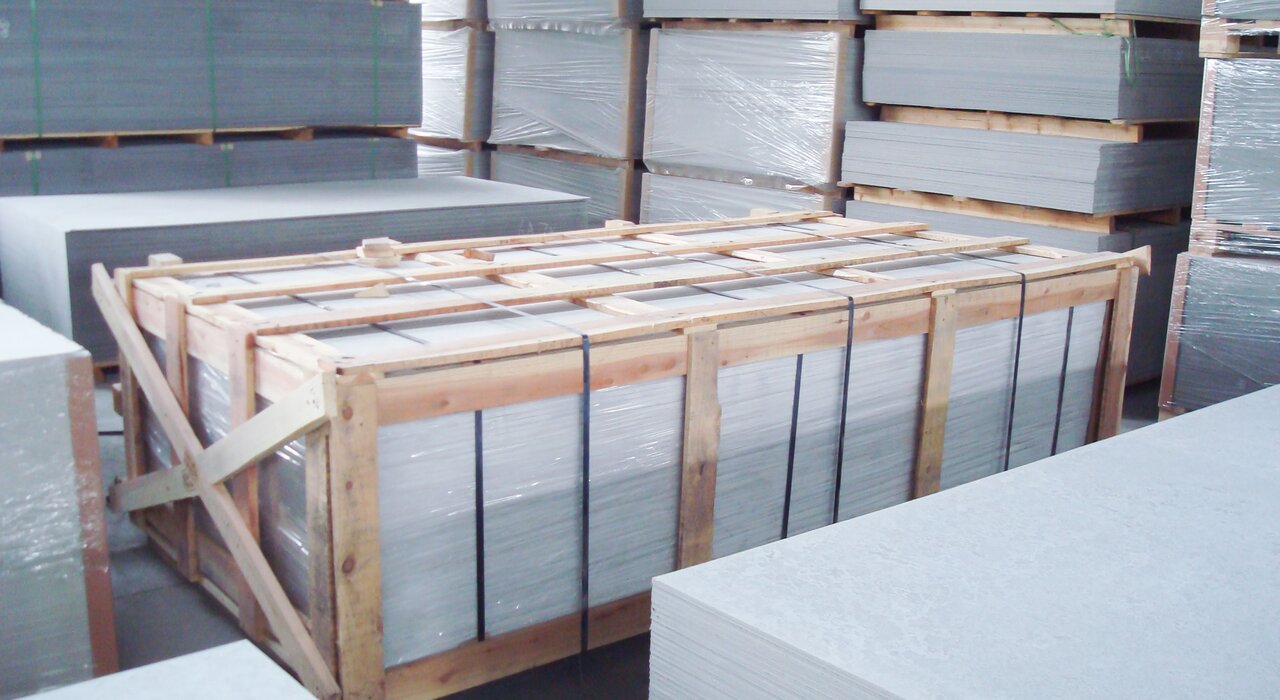
- What are cement boards?
- Why use them in construction?
- Moisture resistance
- Durability and stability
- Fire resistance
- Versatility in applications
- Cost-effectiveness
- How to use cement boards
- Walls and Ceilings
- Floors
- Finishing Touches
- Alternatives to cement boards
- Plywood and OSB (Oriented Strand Board)
- Greenboard
- Fibre cement board
- Gypsum fibre board
- Glass mat gypsum board
Cement boards are a vital component in modern construction, offering durability, resistance to moisture, and a stable base for tiling and other finishes. Their versatility makes them a preferred choice for indoor and outdoor projects, from bathroom walls to exterior cladding. This guide delves into the what, why, and how of using cement boards.
What are cement boards?
Cement boards are a staple in the construction industry and are known for their robustness and versatility. Composed of cement and reinforcing fibres, these boards serve as an ideal substrate for tiles and other finishes due to their moisture resistance and stability. Their construction involves a mix of Portland cement and cellulose or synthetic fibres pressed into sheets. This composition lends the boards' characteristic strength and durability, making them popular for wet areas such as bathrooms and kitchens and exterior applications where weather resistance is crucial. Unlike traditional materials like wood or gypsum board, cement boards do not warp, rot, or degrade when water exposure makes them an excellent option for moisture-prone areas. Their solid construction provides a durable surface that can support the weight of ceramic or stone tiles without bending or breaking. Furthermore, their resistance to fire and pests adds a layer of safety and longevity to construction projects. Available in a range of thicknesses to suit various applications, from underlayment for flooring to backing for wall tiles, cement boards offer a reliable and efficient solution for creating long-lasting, high-quality finishes in construction projects.
Why use them in construction?
Moisture resistance
The primary advantage of cement boards lies in their unparalleled moisture resistance. Traditional building materials like plywood and drywall are susceptible to water damage, leading to mould growth, swelling, and structural integrity loss. Cement boards, however, remain impervious to moisture, making them ideal for wet environments such as bathrooms, kitchens, and laundry rooms. Their ability to withstand prolonged exposure to moisture without deteriorating ensures that structures remain safe and intact over time, reducing the need for frequent repairs or replacements.
Durability and stability
Constructed from a mix of cement and reinforcing fibres, cement boards offer exceptional durability.They resist cracking, breaking, and bending, providing a solid and stable foundation for finishes such as tile, stone, and stucco. This structural integrity is fundamental in flooring applications, where supporting weight without flexing is crucial. The robust nature of cement boards also means they can withstand the rigours of external elements when used in outdoor applications, contributing to their popularity for exterior cladding and underlayment for roofing.
Fire resistance
Another significant benefit of cement boards is their inherent fire resistance. The cementitious nature of these boards makes them non-combustible, providing fire protection to the structures they are used in. This feature is particularly valuable in multi-unit buildings or areas with stringent fire safety regulations.
Versatility in applications
Cement boards are incredibly versatile and suitable for various construction applications. They can be used as a base for tile or stone in flooring, walls, and countertops, as well as in exterior siding and soffits. Their adaptability also extends to underfloor heating systems, which act as a durable thermal mass, distributing heat evenly and efficiently. The ability to use cement boards in various settings and for different purposes makes them an invaluable resource in construction, enabling creative solutions and ensuring long-lasting results.
Cost-effectiveness
Cement boards are a cost-effective option for residential and commercial construction projects, considering their durability, moisture and fire resistance, and versatility. While the initial investment may be higher than some traditional materials, cement boards' longevity, reduced maintenance costs, and versatility provide significant savings over time. Their ease of installation and the ability to prevent common issues associated with water damage further contribute to their overall value.
How to use cement boards
First, select the appropriate thickness and type of cement board for your project. Boards typically range from 6mm to 20mm in thickness. The thicker boards offer more rigidity and are suitable for floors and exteriors.
To cut cement boards, mark your measurement with a pencil and use a scoring knife to score along the line. Then, snap the board along the scored line. A jigsaw with a carbide blade can be used for a more intricate cut.
Walls and Ceilings
- Prepare the Surface: Ensure the studs or joists are level and secure. For walls, install a moisture barrier if needed.
- Fastening: Cement boards can be screwed directly into the studs or joists using corrosion-resistant screws. It's important to leave a small gap between boards and at corners to allow for expansion and contraction.
- Finishing: Fill the joints with a cement-based filler and tape them with fibreglass mesh to ensure a smooth, continuous surface.
Floors
- Preparation: The subfloor must be clean, level, and sturdy. Lay a moisture barrier if applicable.
- Laying Boards: Lay the cement boards on the floor, staggering the joints for added stability. Secure them with screws to the subfloor.
- Sealing Joints: Like with walls, fill the gaps with a cement-based filler and tape them with fibreglass mesh.
Finishing Touches
Once installed and sealed, the surface can be tiled or finished as desired. For optimal results, ensure that the adhesive and grout are compatible with cement boards.
Alternatives to cement boards
While cement boards are favoured for their moisture resistance and durability, several other materials can be suitable substitutes depending on the application.
Plywood and OSB (Oriented Strand Board)
For applications where moisture is less of a concern, plywood and OSB offer structural strength and ease of installation. Both are made from wood, with plywood consisting of thin layers of wood veneer glued together. OSB is composed of pressed wood strands. These materials are commonly used as subfloors or sheathing in dry areas. However, they're unsuitable for high-moisture environments unless treated or covered with a waterproof membrane.
Greenboard
Greenboard is a type of drywall treated to be more moisture-resistant than regular drywall. It's identifiable by its green paper covering. While greenboard can withstand humidity and occasional water splashes, it's not waterproof and should not be used in places with direct water contact, such as shower enclosures. It's more suitable for areas with elevated moisture levels, like bathrooms and kitchens, where it's not exposed directly to water.
Fibre cement board
Fibre cement board is a more durable alternative that contains cement but also reinforces fibres made from cellulose. It's used in interior and exterior applications and offers excellent moisture, durability, and fire resistance. While similar to cement board, fibre cement is often used for siding, cladding, and façade projects due to its aesthetic appeal and longevity.
Gypsum fibre board
Gypsum fibre board combines gypsum with cellulose fibres from recycled paper. It's denser and more durable than standard drywall, making it suitable for residential and commercial construction as wall and ceiling panels. Though not as resistant to moisture as cement board, gypsum fibre board can be used in areas with lower moisture exposure and provides a smooth finish for paint or wallpaper.
Glass mat gypsum board
This material features a water-resistant gypsum core covered with fibreglass mats instead of the traditional paper-facing. It's designed for use in areas prone to moisture and can withstand exposure to water better than a greenboard. However, like a greenboard, it shouldn't be used in areas with direct water contact.