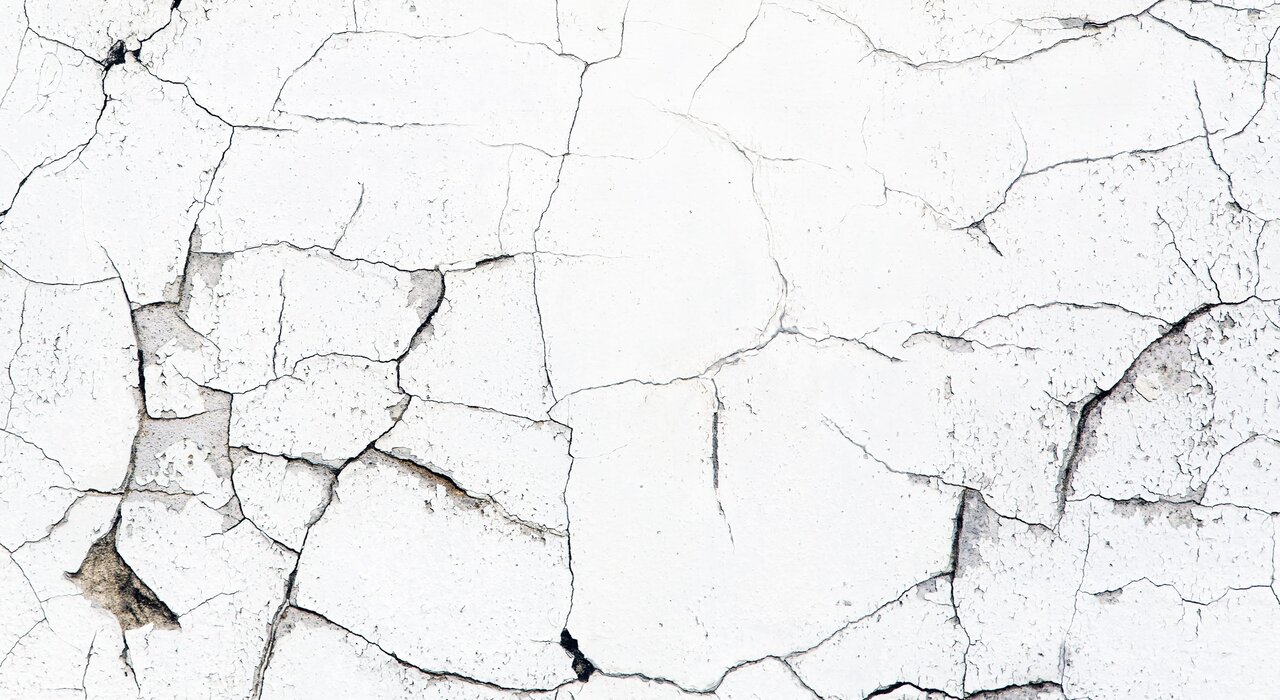
Render cracks due to many reasons. Typically, render provides the building fabric with protection against the elements while also providing an aesthetically pleasing finish. Render covers up the use of cheaper building materials such as blockwork.
Unfortunately, a common stereotype of render is that it is liable to experience cracking. This is a huge concern for many of our customers, who want to invest in a new render façade but don’t want to find that a few years (or even months) down the line their investment isn’t holding true to its promise.
Cracks are the effect of a number of underlying problems, and if left to their own devices they can escalate a situation from bad to worse by drawing water through the building. There are a number of reasons that render may crack, and in this blog post we’re going to be looking into these reasons.
Weathering
First thing’s first, is your render really old? Render does in fact have a lifespan, especially sand and cement render. Cracking is going to be inevitable due to the effect of weathering. Sand and cement renders are especially susceptible to weathering.
When driving rain, snow, frost and more are constantly attacking the exterior of your building, it’s likely that you will experience some kind of negative impact. This is particularly true for sand and cement render, which is incredibly solid, unforgiving, and prone to absorbing water. The age of the render may be the reason for the wear and tear; our silicone renders have a lifespan of 25 years.
Incorrect materials for the substrate
A study of materials incorrect for the substrate can be found here. The resulting finish was a cracked mess within weeks. The reason for the cracked render is that high performance blockwork (this includes Ziegel blocks, AAC, Thermalite etc.) tends to be very soft and malleable. On the other hand, sand and cement is incredibly solid.
The phrase ‘opposites attract’ is not true in the case of renders and substrates. When choosing a render for your property, it’s imperative that it compliments the substrate. This could be the reason your render is cracking. An installer should be able to advise you on the best type of render for the building fabric.
Poor quality of workmanship - poor sealing at junctures, incorrect movement joints
A good quality installation from a knowledgeable installer can make all the difference to the durability of your installation. A trusted installer will ensure that correct reinforcement is applied around the weaker areas of a structure. Crucially around movement joints and reveals.
The render needs to be able to replicate and compensate for movements within the underlying substrate, otherwise it will crack. The cracks would be caused by not taking this into consideration.
The render dried out too fast
Most common with dry-mix renders, if the water evaporates from the material too quickly it doesn’t leave enough time for the render to bond properly and the surface colour can appear patchy and discoloured.
A render that has dried out too fast is a dehydrated, weak surface and cracking is therefore inevitable. The render is applied in moderate temperatures and away from the direct glare of the sun. For dry-mix renders if the mixture appears to be drying too fast simply sprinkle it with water as needed.
Fibreglass mesh
Best practice for rendering is to embed fibreglass mesh within the basecoat layer. The mesh reinforces the surface of the basecoat and increases tensile strength. The layers create a strong base as they are overlapped; any movement of the building fabric will be absorbed by the fibreglass mesh as a result.
Unfortunately, if fibreglass mesh is not embedded in the process of rendering, the whole system will be prone to cracking.
Structural problems
Sometimes, the render is not at fault. Underlying structural problems may well be surfacing, causing cracked render. The structural problems can be numerous and difficult to pin down, whether it’s differential movement between an extension and the main house or due to water and rust.
Rising damp
Rising damp is the fear of all property owners as it’s often difficult to catch and identify. It’s relatively rare, but rising damp is essentially when water travels from the ground up through the walls by capillary action, causing bulging in the walls and floor boards and general structural damage. The structural damage that rising damp can cause is what encourages cracks to form in the external render. You will most likely notice signs of rising damp not just in your render but internally as well.
Leave a comment down below if you’ve experienced cracking in your render and how you fixed the problem!