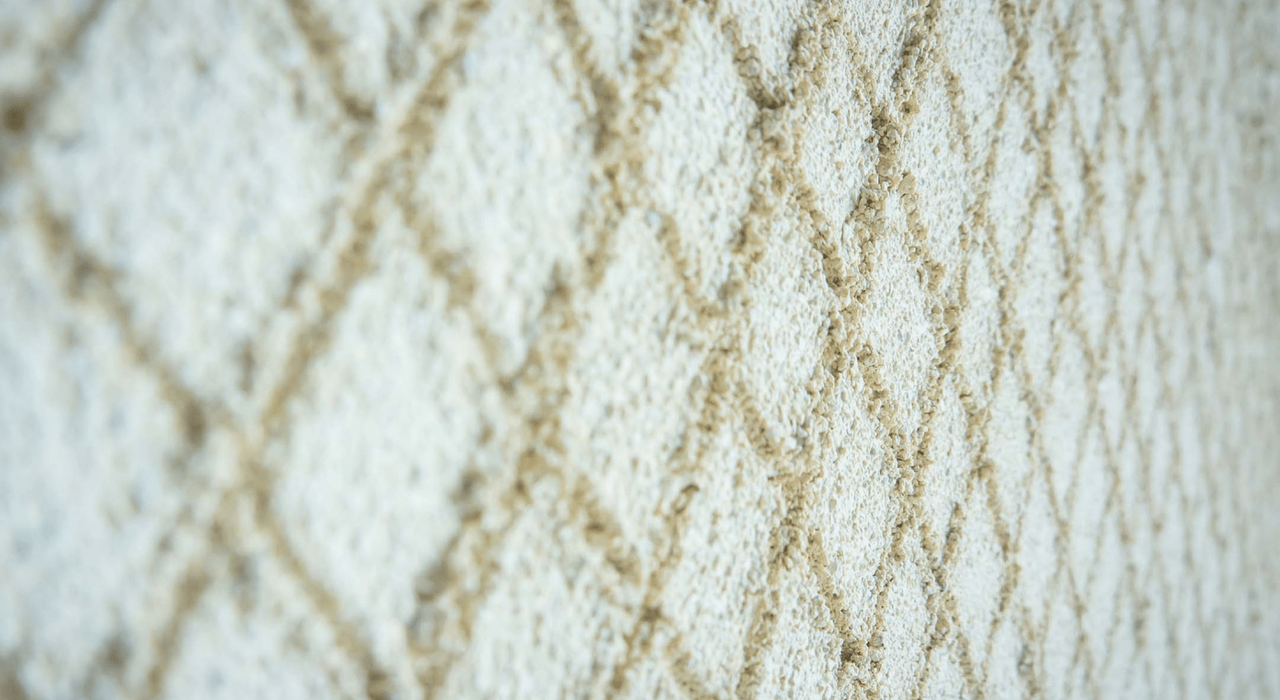
Table of contents
- Lime rendering origins
- Non-hydraulic lime
- Why use lime render?
- Three-coat lime render
- How to apply one-coat lime render
Lime render is an innately natural product and our new Lime Render will form the crux of the heritage range of products. The heritage range harks back to traditional building techniques and styles, with a great emphasis on environmental and ecological sustainability. At EWI Store, sustainability is at the forefront of our consciousness. The introduction of a heritage range deepens our commitment to sustainable practices. Moreover, this is not just limited to the transactional stage of the process; lime renders and its lifespan is intrinsically linked with lower embodied and operational carbon.
Lime rendering origins
The first mentions of lime mortar date back to 6,500 BC in the Indus Valley, with further records mentioning lime render around 2,500 BC in Egypt. The process of creating lime render back then was incredibly simple as a combination of lime and sand would react with carbon dioxide and proceed to harden. This would form limestone. Roman engineers took this process further by adding volcanic ash or brick dust, allowing the mixture to harden at an accelerated rate. The resulting mixture was hydraulic mortars.
Hydraulicity is the ability of a mixture to set underwater without exposure to air. As a result, Romans could use the new hydraulic lime render in cisterns and aqueducts. The development was crucial to the growth of civil engineering and consequent technological advancements. Roman aqueducts could ferry water across whole cities, supplying clean water to the whole city.
Testaments to the durability of lime render are still seen today, as many Roman aqueducts are still standing. Moreover, the Acqua Vergine still acts as a functioning aqueduct, bringing water to certain Roman fountains.
Lime render and cement
Lime renders nowadays comprise hydraulic lime, water, and an aggregate such as sand. It is beneficial for the sand to be ultra-fine to prevent any issues with consistency upon mixing. As a result of its origins, lime render is primarily for the conservation of old buildings and in the construction of new buildings that mimic heritage features. The advent of Portland cement in the 19th century supplanted lime render as the primary option in construction. However, cementitious mixtures tend to be extremely durable, to the point of being inflexible. They are also much heavier, therefore not suitable for the refurbishment of older, softer building materials.
Cement tends to be far less breathable; it evaporates water less than bricks, for example, exasperating any dampness issues. Spalling is an issue that affects cement and concrete plasters as they are susceptible to freeze-thaw cycles. These cycles cause rapid expansion and contraction. Chunks of the material can subsequently delaminate from the substrate.
Hydraulic lime
Lime splits into hydraulic and non-hydraulic lime and as established, hydraulicity is the ability to set underwater without exposure to air. Natural hydraulic lime (NHL) comes in three strength grades, labelled as feebly, moderately, and eminently hydraulic. The number indicates the compressive strength of the relative lime. Hydraulic lime is produced from limestones with naturally occurring impurities. It sets through the process of hydrolysis, a chemical reaction in which a molecule of water breaks one or more chemical bonds. In comparison to non-hydraulic lime, it has a faster initial set and greater compressive strength. Due to the faster set, it sets in extreme conditions like underwater.
As hydraulic lime reacts with water, the product is supplied as a dry powder to building sites. The process of producing a usable lime render on-site includes dry-slaking.
Type of NHL | Description | Masonry Type | Exposure | Setting | Use |
---|---|---|---|---|---|
NHL 2 | Feebly hydraulic | Soft, permeable masonry | Minimal | Softer, slow setting | Internal with concern for the conservation of soft & deteriorating stones and bricks |
NHL 3.5 | Moderately hydraulic | Medium density masonry | Moderate | Regular setting | Use when NHL 2 and NHL 5 are not specifically required |
NHL 5 | Eminently hydraulic | Dense, impermeable density | Severe | Stronger, faster setting | Dense, durable, or impermeable materials |
Hardening
Hydraulic Lime hardens through a combination of carbonation and a chemical reaction with water, known as hydraulic action. There are three drying processes for hydraulic lime:
- Initial set: The initial set, when the lime mortar or render starts to firm up and lose its plasticity, can take anywhere from a few hours to a day or two, depending on the specific hydraulic lime used and the conditions.
- Final set: The final set, when the lime mortar or render has hardened enough to be self-supporting, usually occurs within 1 to 7 days, depending on the hydraulic lime class, mix proportions, and environmental conditions.
- Full cure: Although hydraulic lime hardens more quickly than non-hydraulic lime, it still takes time to achieve its full strength and cure completely. This can range from a few weeks to several months, with strength continuing to develop even after a year.
Non-hydraulic lime
Non-hydraulic lime differs in several ways, perhaps most noticeably in the way it looks. It comes in the form of white putty and is also manufactured from limestone. However, it is burned in a kiln and sets by a completely different chemical process. That process is carbonation, therefore it requires air to draw the carbon particles in. As the chemical process is different, non-hydraulic lime cannot be set underwater, is much softer for longer, and sets much slower than hydraulic lime. As the lime is much softer, it allows for sufficient movement in conservation projects, however, it can be much harder to use on-site. The initial outlay savings are therefore offset by the increased labour costs.
The absorption of carbon dioxide is important for lime renders. Non-hydraulic lime render is particularly adept at absorbing carbon dioxide as it requires it to set properly. The material absorbs more carbon dioxide during the longer setting period. Consequently, taking far more out of the atmosphere.
The installation timeframe and difficulty of use are just some of the reasons why hydraulic lime is better than non-hydraulic lime. Hydraulic lime provides a faster initial set and greater compressive strength. When working, hydraulic lime is similar to cement therefore less specialised skill is required.
Suction control and bonding
It is vitally important to check the suction of the substrate before application; either extreme suction can result in a weak bond caused by rapid de-maturing of the lime render. The final result is a weak and powdery façade leading to later failure and separation.
Either way, wetting stabilises a substrate. Dense or impervious masonry requires minimal misting, whilst very porous surfaces require far more wetting. A certain amount of suction is required for lime render to adhere and stiffen. The amount of saturation required is determined by a skilled installer.
Why use lime render?
One of the primary reasons for using lime render is breathability. The breathability of lime render refers to its ability to allow water vapour to pass through its structure, facilitating the movement of moisture in and out of a building's walls. This permeability is a crucial characteristic of lime render, providing several advantages over less breathable materials, such as cement-based renders.
Factors Contributing to Breathability
- Porosity: Lime render's breathability is primarily due to its porous structure. The pores within the material create channels for water vapour to move through, allowing moisture to escape from the interior of a building and evaporate on the surface. This porosity is influenced by several factors, including the type of lime, the sand used in the mix, and the application techniques.
- Hygroscopicity: Lime render is hygroscopic, meaning it can absorb and release moisture from the surrounding environment. This characteristic helps regulate humidity levels within a building, as the material can take in moisture when the air is damp and release it when it is dry. The hygroscopic nature of lime render is an essential component of its breathability.
- Capillarity: Capillarity refers to the movement of moisture through a material due to the surface tension of the liquid and the adhesive forces between the liquid and the material's structure. In lime render, capillary action facilitates the transport of moisture through the material, allowing it to evaporate on the surface and further enhancing its breathability.
Three-coat lime render
Three-coat lime render is for traditional lime render which is a highly skilled process as you have to be able to "read" the render and decide when it is dry enough for the next coat.
The starting point for any rendering project is the selection of your product. You must also consider the surface of the substrate as some substrates may be more structurally sound than others. The considerations for the products revolve around strength, performance, and workability.
As with any rendering, the substrate needs to be cleaned and free of all dust. A sound mechanical key is also crucial as it aids adhesion, therefore any overly smooth substrates should be scraped.
Lime render is notoriously temperamental, especially in its infancy. It can fail for a multitude of reasons, including excessive shrinkage, drying back too quickly, or weather damage whilst the render is still setting. Shrinkage is inevitable with lime render, however, excessive shrinkage is combated with a plasterer's float. Drying out too quickly and carbonising are also very different. Extremes of weather also have an impact on the durability and long-term performance of lime render. Therefore, take precautions like sheltering the area, especially in the first 14 days of the setting process.
Whilst three-coat lime render is traditional, it is an incredibly laborious process. At EWI Store, we stock a one-coat NHL 3.5 lime render, which offers the same breathability and performance, paired with a much easier installation process.
How to apply one-coat lime render
One-coat lime render is applied in one pass and levelled with a straight edge. Approximately 1.5 hours after application, use a sponge float the surface to create a light, creamy texture. Consequently, a steel trowel creates a smooth finish. There should still be no overworking as it can lead to cracking and excessive shrinkage.
Points to remember about lime render
There are several points to take away when you think about lime render:
- Mortars should be sacrificial
- Mortar is softer than masonry
- Softer lime mortar will absorb & evaporate
- Breathable
- Does not leach damaging chemicals
- Accommodate movement & thermal expansion
- Mortar should be as soft as it needs to be but no softer
- Lime absorbs carbon dioxide
- Lower embodied and operational carbon
Lime render is a fantastic option for renovation projects on older properties. If you have any other questions about lime render, leave us a comment!