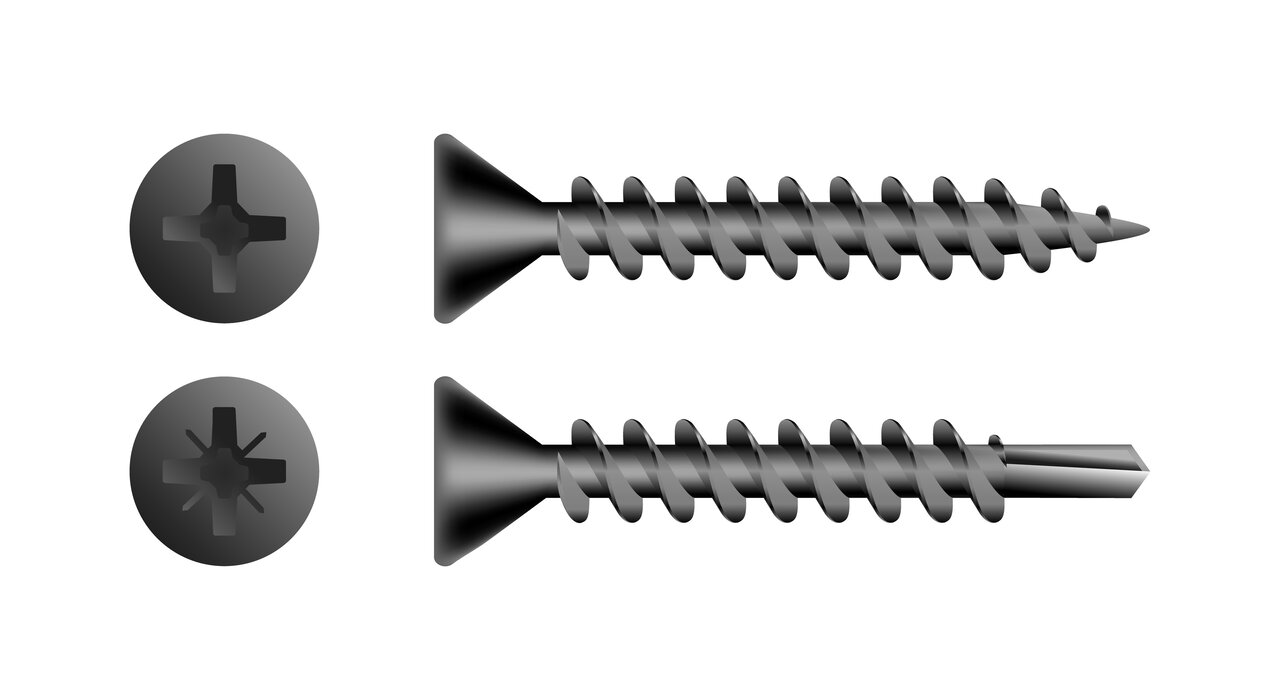
Even though self-tapping screws are commonly found and used in industrial, commercial, and construction fields, many individuals often confuse them with self-drilling screws. The confusion can be attributed to the fact that self-drilling screws are a subset of self-tapping screws. All self-drilling screws are self-tapping BUT all self-tappers are NOT self-drillers.
Let's delve deeper into these two distinct products to clear up any confusion.
Self-Tapping Screws
Self-tapping screws go by many other names, including metal screws, tapper screws, sheet metal screws, and tapping screws.
These screws feature differently shaped tips, such as pointed, blunt, or flat, and can be categorised as thread-forming, thread-cutting, or thread-rolling. If a screw has a pointed end, it is thread-cutting and can create threads in a pre-drilled hole. In contrast, a flat-tip screw is thread-rolling, rolling or extruding threads, and causing no gap between the screw and the material.
When selecting the right self-tapping screw, the material it will be applied on should be taken into account. Various types of self-tapping screws are designed for specific materials like wood, metal, or plastic. Factors such as the size and length of the screw and the amount of torque needed should also be considered.
Self-tapping screws are generally easy to use with a range of tools, such as power drills and screwdrivers. Over-tightening, however, can lead to thread stripping and weaken the screw's grip. It's also crucial to ensure that the pilot hole, where the screw will be inserted, is of the right size and shape for proper thread formation and grip.
A significant benefit of self-tapping screws is that they don't need pre-tapping. This is the procedure of forming threads before screw insertion, thus saving time and labour costs. They can also be used on materials too thin or brittle for pre-tapping, increasing their versatility in various applications. Proper hole size is critical, as an oversized hole can make the screw loose and unsecured. Alternatively, a hole too small can break the screw or cause the material to split.
Importance of pilot holes
The key difference between self-tapping and self-drilling screws is that self-tapping screws require a pre-drilled or pre-punched pilot hole to go through the metal. Pilot holes are crucial for self-tapping screws for several reasons. The installation becomes easier and reduces material damage, especially when the material is brittle. Moreover, a pilot hole reduces the stripping of the screw head and increases accuracy.
Self-tapping screws can be applied on metals, diverse plastics, and cast or forged materials like iron, brass, or aluminium. They're suitable for surfaces where you cannot secure the rear end with a nut. They're often used in tasks like fastening aluminium parts, fixing metal brackets to wood, or putting screws into plastic casings.
In summary, self-tapping screws are adaptable, convenient, and can create threads in various materials. They're easy to use, save time and labour, and are suitable for many applications. The material, size, length, and thread pattern of the screw, along with correct installation techniques, can ensure a secure and reliable grip.
Self-Drilling Screws
Self-drilling screws can be recognised by their twisted drill-like point. They are often referred to as Tek Screws, named after the brand that made them famous.
Like self-tapping screws, self-drilling screws are easy to install with various tools and can lose grip strength if over-tightened. The pilot hole's size and shape, where the screw is inserted, should be correct to ensure proper thread formation and grip.
The lengths of these screws can differ, but their drill points follow a standard, identified by numbers (1 to 5), determining their length and thickness. Common head and drive styles for self-drilling screws include Phillips, hex, or square.
Unlike self-tapping screws, self-drilling screws do not require a pilot hole. They can drill, tap, and fasten in a single operation, saving the extra step of drilling before fastening.
The selection of the right self-drilling screw also requires considering the material it will be used on. Various types of self-drilling screws are designed for specific materials like wood, metal, or plastic. The size, length of the screw, and the amount of torque needed should also be considered.
Different screw tips
Another consideration when using self-drilling screws is the screw tip. Various tip styles, such as fluted, split-point, or self-centring tips, are designed to guide the screw through the material without drifting. This could result in a poorly formed hole or damaged material.
These screws can fasten metal to metal, and wood to metal, and are effective with light, low-density materials. They have more specialised applications than self-tapping screws. They are suitable for metal building and light gauge metal assemblies. Point #5 is even capable of fastening half-inch steel sheets.
Self-drilling screws find use in HVAC applications, cladding, metal roofing, steel framing, and other general construction jobs.
To conclude, self-drilling screws offer a convenient method for creating threads and drilling holes in one step. They're easy to install, save time and labour, and are suitable for many applications. The material, size, length, and tip of the screw, along with correct installation techniques, can ensure a secure and reliable grip.
Similarities and differences
The major similarity between these two types of screws is their ability to form threads as they penetrate the material they're applied to. Both are capable of attaching steel to steel and steel to wood when rivets or nuts and bolts aren't viable.
Among these two, self-drilling screws have two distinct benefits. They save time and costs during assembly, and they reduce installation errors, which often occur if pre-drilled holes are of incorrect size.
If you have any questions about either screw, leave us a comment below!