Exclusive Offers – While Stocks Last!
Log in to save items on your shopping lists and access them on all your devices. Guest lists are deleted after 90 days.
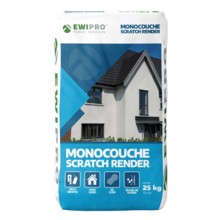
SALE
Brand: EWI Pro
FROM
£12.59
Incl. VAT
FROM
£10.49
Excl. VAT
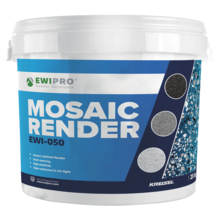
SALE
Brand: EWI Pro
FROM
£77.51
Incl. VAT
FROM
£64.59
Excl. VAT
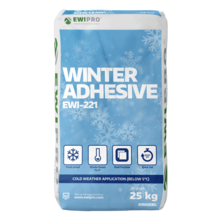
SALE
Brand: EWI Pro
£11.99
Incl. VAT
£9.99
Excl. VAT
£19.01
Incl. VAT (regular price)
£15.84
Excl. VAT (regular price)
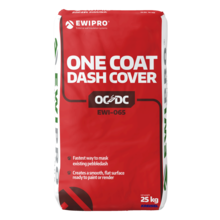
SALE
Brand: EWI Pro
£15.89
Incl. VAT
£13.24
Excl. VAT
£21.19
Incl. VAT (regular price)
£17.66
Excl. VAT (regular price)
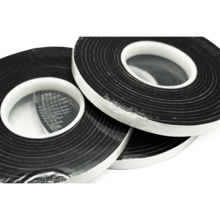
SALE
Brand: Lynvale
£11.74
Incl. VAT
£9.78
Excl. VAT
£15.65
Incl. VAT (regular price)
£13.04
Excl. VAT (regular price)
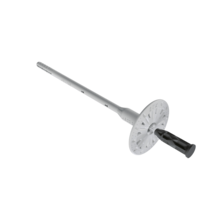
EWI Pro - Metal Hammer Fixing - 8mm
SELECT OPTIONS
Brand: EWI Pro
FROM
£15.24
Incl. VAT
FROM
£12.70
Excl. VAT
Tried, Tested & Trusted – Our Customer Favourites
Log in to save items on your shopping lists and access them on all your devices. Guest lists are deleted after 90 days.
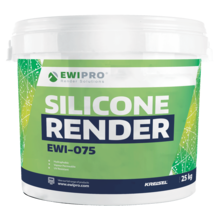
Silicone Render (EWI-075) – 25KG
SELECT OPTIONS
Brand: EWI Pro
FROM
£83.99
Incl. VAT
FROM
£69.99
Excl. VAT
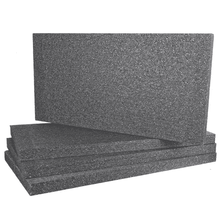
EPS Insulation (1 board = 0.72m²)
SELECT OPTIONS
Brand: Styrene
FROM
£2.60
Incl. VAT
FROM
£2.17
Excl. VAT
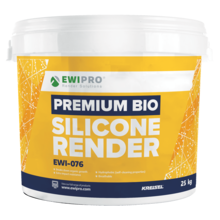
Premium Bio Silicone Render (EWI-076) - 25kg
SELECT OPTIONS
Brand: EWI Pro
FROM
£113.39
Incl. VAT
FROM
£94.49
Excl. VAT
Exclusive
trade account discounts
Dedicated
account manager
Generous
credit terms