Popular Products
Log in to save items on your shopping lists and access them on all your devices. Guest lists are deleted after 90 days.
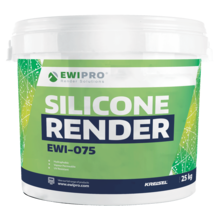
Silicone Render (EWI-075) – 25KG
SELECT OPTIONS
Brand: EWI Pro
FROM
£83.99
Incl. VAT
FROM
£69.99
Excl. VAT
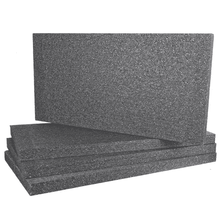
EPS Insulation (1 board = 0.72m²)
SELECT OPTIONS
Brand: EWI Pro
FROM
£2.60
Incl. VAT
FROM
£2.17
Excl. VAT
Exclusive
trade account discounts
Dedicated
account manager
Generous
credit terms